Value chain management
<Manufacturing / Quality Assurance / Procurement>
With the aim of producing high-quality products with short lead times, MAX is building a strong production infrastructure based on a global production control system, 5S activities with full participation, and a traceability system that utilizes IT.
MAX's domestic manufacturing sites are Tamamura Factory, Fujioka Factory, Kuragano Factory, and Yoshii Factory in Gunma Prefecture. Our group companies have MAX Joban Co., Ltd. in Ibaraki Prefecture and Kawamura Cycle Co., Ltd. in Hyogo Prefecture. Overseas, we conduct manufacturing in Thailand, Malaysia, and China (Shenzhen and Suzhou). Kawamura Cycle Co., Ltd. also operates a Chinese factory in the city of Zhangzhou, Fujian Province, China.
Domestic | Tamamura Factory | Nailers, air compressors, rebar tying tools, auto-staplers, electronic office equipment, etc. |
---|---|---|
Fujioka Factory | Staples for staplers, staplers for auto-staplers, consumables such as wires for rebar tying tools, etc. | |
Kuragano Factory | Staplers, air compressor tanks, etc. | |
Yoshii Factory | Bathroom heaters, ventilators and dehumidifiers, total heat exchange type full-building 24-hour ventilation systems, etc. | |
MAX Joban Co., Ltd. | Nails, wires for rebar tying tools, etc. | |
Kawamura Cycle Co., Ltd. | Wheelchairs, welfare products, etc. | |
Overseas | MAX (THAILAND)CO.,LTD. | Staplers, nailers, wires for rebar tying tools, auto-staplers, tapener, etc. |
MAX FASTENERS(M) SDN.BHD. | Staplers, staples for staplers, etc. | |
MAX ELECTRONICS MACHINE CO., (SHENZHEN) LTD. | Auto-staplers, electronic office equipment, etc. | |
MAX ELECTRONICS MACHINE (SUZHOU) CO., LTD. | Bathroom heaters, ventilators and dehumidifiers, etc. | |
ZHANGZHOU LEATAI MEDICAL INSTRUMENTS CO., LTD. | Wheelchairs, welfare products, etc. |
MAX is committed to ensuring responsible procurement in order to realize a sustainable society.
We consider our suppliers of raw materials, parts, and other materials as important partners and strive to build relationships of trust through open, fair, and impartial transactions, and we promote responsible procurement throughout the supply chain.
Specifically, we have formulated the "MAX Group Sustainability Guidelines for Business Partners" and ask our suppliers to thoroughly respect human rights, protect the environment, and comply with laws and regulations throughout the entire supply chain involved in procurement, including suppliers of our suppliers.
In addition, we will visit our suppliers' factories and other sites as necessary to confirm compliance with these guidelines and for mutual communication. In some cases, this may take the form of a third-party audit.
In the unlikely event that a problem that violates these guidelines should arise, we request that it be promptly reported and that efforts be made to remedy the situation. If appropriate improvements are not made by the supplier, we may take action such as suspending transactions.
Improvement of Quality and Cost Through 5S Activities
MAX's factories hold 5S activities with total participation. At our factories in Japan and overseas, teams hold morning meetings to share issues and results by discussing quality and costs. By conducting 5S patrols, we are able to identify dangerous areas and improve the working environment. In Japan, the 5S study sessions are held once every three months under the leadership of the General Manager of the Production Division. At the sessions, the results of activities by each team are announced and evaluated. Indirect departments also participate in the 5S study sessions, which leads to business reforms such as reducing the number of documents.
Quality Assurance Through Traceability
MAX operates a traceability system that utilizes IT. At our domestic and overseas factories, we conduct inspections in all manufacturing processes, from receiving parts from suppliers to shelving, picking, assembling, and shipping. These efforts contribute to quality assurance of products and strengthening of production systems.
Supply Chain Support for Customers
MAX is taking measures such as increasing the number of manufacturing sites so that we can maintain the supply of products which are important for our customers and our business continuity even in the event of a risk such as a large-scale disaster. We are also taking risk measures in terms of our suppliers, such as increasing the number of suppliers of important parts.
Logistics
MAX possesses eleven delivery centers in Japan for delivering products to our customers in a timely manner. MAX Logistics Warehouse Co., Ltd. handles storage and transportation management for products made in Japan. Actual transportation for both domestic and overseas product is outsourced to an external transportation company.
<Product Development / Intellectual Property>
Achieving "Only One" and "No. 1" Through Product Development and Intellectual Property
MAX has created a vast number of unique products by fusing user needs and technological seeds based on our thorough on-site principle, and by establishing a consistent story from product concept planning to practical application by the designer. In the intellectual property department, we have acquired the intellectual property rights of our invented technology that realizes the selling point of the product, and have constructed a strong patent network so that competitors cannot implement our selling points. Through these efforts, our products maintain the position as "No. 1."
Promoting Commercialization Through Development and Intellectual Property
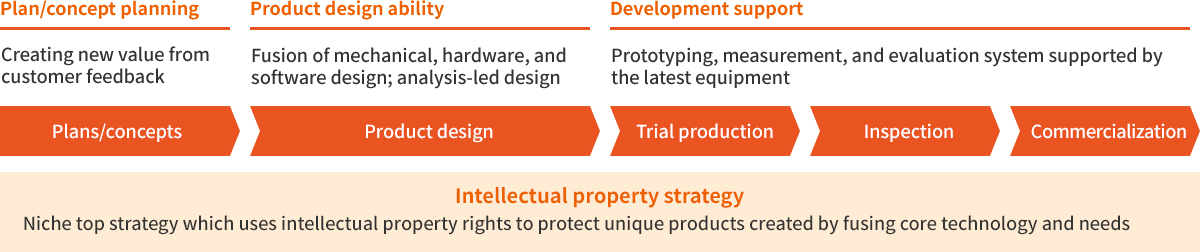
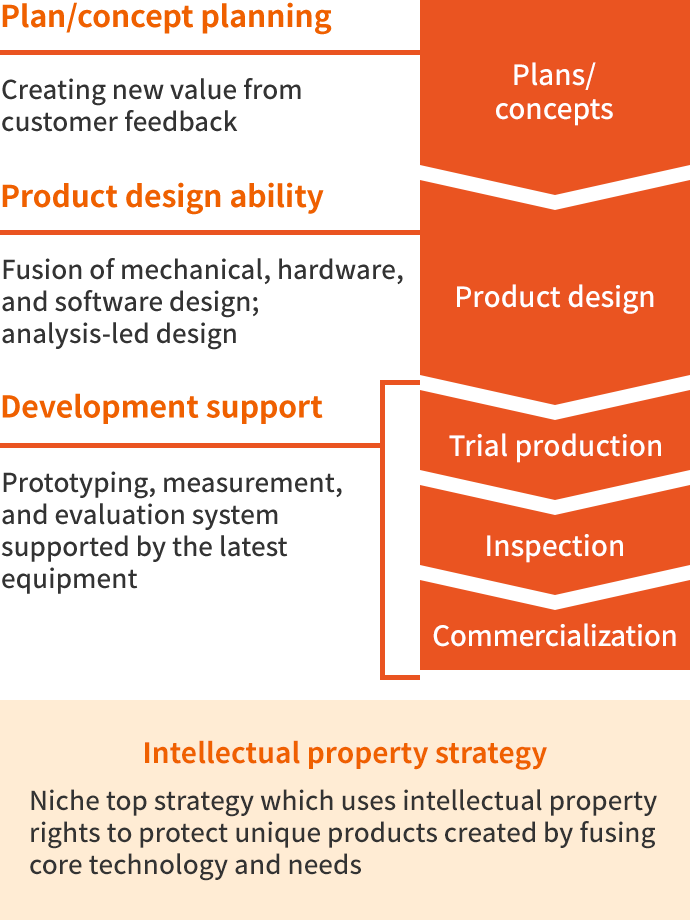
Example of the Rebar Tying Tool TWINTIER
In 1993, MAX launched the world's first rechargeable rebar tying tool. Since then, we have been expanding the market by making improvements while listening to on-site opinions. In 2017, by launching the TWINTIER product that enables faster and stronger tying by simultaneously discharging two wires, we established our position as the "only one" and "No. 1" in the global market.
Direction of Product Development
MAX possesses engineers skilled in mechanical design, and electrical, electronic, and software design. In mechanical design, we are using 3D design to strengthen structural analysis and dynamic analysis. In electrical, electronic, and software design, we are strengthening mechatronics control such as magnetic analysis and high-speed signal processing, and we are focusing on developing solutions using IoT technology.
Furthermore, in addition to expanding prototype processing equipment such as 3D metal/plastic modeling and CAM processing, we are working to rationalize research and design work through measures such as introducing an anechoic chamber, a large environmental test room, and the latest measurement experiment equipment. Through these measures, we are improving the efficiency of design and development.
The direction of product development at MAX is based on three points: (1) Creating new products that will lead to the establishment and expansion of new businesses, (2) Expanding business volume by strengthening the competitiveness of existing products, and (3) Improving design quality in upstream product development processes and shortening the lead time of the entire product development process. In fiscal 2024, R&D expenses were 4.4 billion yen and the R&D ratio was 4.8%.
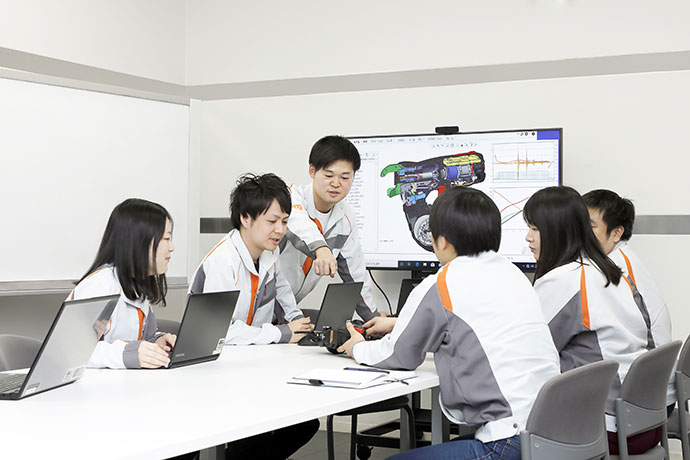
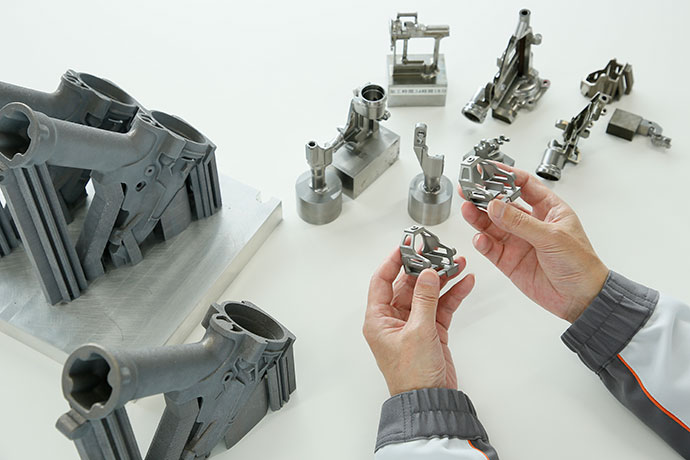
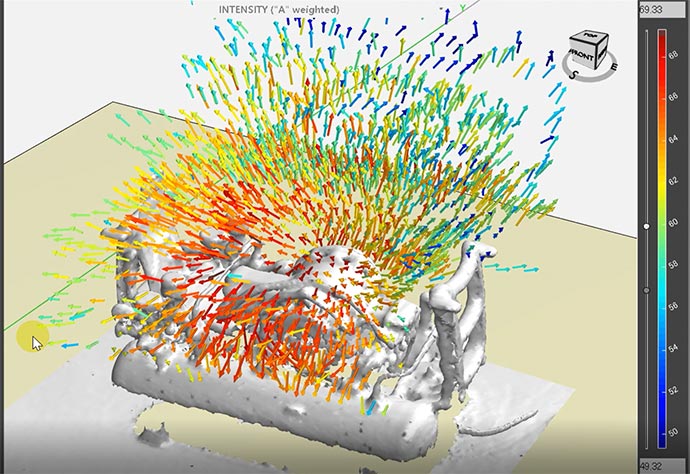
Development Process for New Products
In order to provide products which are highly safe for customers and the environment, MAX designs and controls our products using original standards based on ISO 9001 and ISO 14001. Our product tests include environmental tests, noise and vibration tests, radio wave interference tests, material strength tests, drop tests, and insulation tests and temperature rise tests conducted in the usage environment. These tests are conducted using MAX's original standards based on market information and changes in standards such as CE, EN, ISO, and JIS.
Product Development for Solving Social Issues (Environmental Conservation)
MAX conducts product assessment based on its own standards for recycling, resource saving, energy saving, etc., including regulations on prohibited substances that exceed the RoHS Directive. Furthermore, from fiscal 2019, we have set goals that incorporate the perspective of the SDGs (Sustainable Development Goals).
Product Development for Solving Social Issues (Decreasing Labor Force)
MAX develops original technologies to accelerate technological development such as labor saving, automation, and robotization in order to solve social issues such as the decreasing labor force in developed countries. We also promote open innovation with universities and external institutions. In 2020, we launched the TWINTIER Walker Model, which is a rebar tying tool that can be used while standing without bending over. MAX is developing products that contribute to improving the working environment and increasing work efficiency. For example, we are analyzing a model of the human body to quantify the burden on the human body.
Protection of Intellectual Property
In order to establish the position of MAX's "only one" and "No. 1" products, we are making the protection of intellectual property as a priority issue.
MAX grasps the legal systems of each country in the world, and works with patent attorneys and lawyers to create strong rights that match the laws of each country. We also monitor counterfeit and infringing products, and work with patent attorneys and lawyers in each country to protect MAX's intellectual property.
<Sales / Services>
MAX operates various businesses such as office products (staplers, label-making machines, etc.), industrial equipment products (nailers, rebar tying tools, etc.), branch induction binders for horticulture, and bathroom heaters, ventilators and dehumidifiers. For sales and services of each product, MAX's basic policy is to talk face-to-face with customers by directly visiting customer sites. Additionally, in regards to employee evaluation, we foster a culture that goes beyond quantitative evaluation of areas such as sales to also consider processes which lead to solving customer issues and making new proposals.
Sharing Customers' Opinions
Customer feedback from MAX's sales, product planning, and customer support departments is shared at monthly meetings to help solve problems. The information is also posted on the intranet so that it can be viewed across departments.
Initiatives for Improving Quality
MAX sets several months following the launch of a new product as a "hotline" period. During this period, employees from the product development department and quality assurance department visit the customer, and MAX constructs mechanisms for immediate response to needs and issues. In addition to improving customer satisfaction, these efforts also prevent occurrences such as recalls. Even during normal support, if a problem such as failure occurs, MAX also checks the usage status at the customer at the site. Such efforts lead to solutions for the fundamental problem.
Raising Awareness Toward Safe Usage
While striving to improve product safety, MAX also produces and distributes videos on the safe usage of nailers and rebar tying tools, and holds safety seminars.
Proposals Based on Extensive Knowledge
MAX makes proposals based on our extensive knowledge of our customers' work. In the AF (Agriculture & Food) field which includes products such as branch induction binders for horticulture, we user our knowledge of fruit and vegetable varieties, cultivation methods, and distribution to make proposals which contribute to the entire supply chain, from farmers to supermarkets.