Solving Social Issues Through Our Activities
Our jobsite-oriented principle helps to solve social issues.
MAX's strict jobsite-oriented attitude towards manufacturing has created a number of "products only we can create" and "our unique and quality products" in various niche markets, and such products have contributed to creating healthy, safe and secure living and working environments.
Reducing physical burden and providing solutions for labor shortages
Rebar Tying Tool "Stand-up TWINTIER"
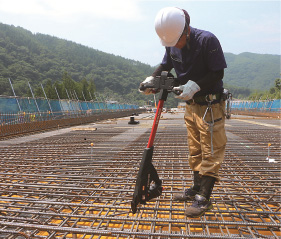
Before MAX started to sell the world's first battery-operated rebar tying tool in 1993,rebar tying work
had been done manually by using pliers. Aer several model changes, we developed the TWINTIER mechanism in 2017 which ties concrete reinforcing bars with two wires. Because we succeeded in improving its binding force and shortening its tying time to 0.7 seconds, our TWINTIER has established an overwhelming leading position in the market. Furthermore, in 2020, we started to sell the "Stand Up TWINTIER," which allows its user to conduct tying while standing and walking. Since rebar tying work
is often conducted under the scorching sun, in this current environment where aging and the reduction of reinforcement workers are ongoing, we believe that "TWINTIERs" are an innovative product that can reduce the physical burden and working time of workers at the same time.
NETIS (New Technology Information System) is a database operated by the Ministry of Land, Infrastructure, Transport and Tourism for the purpose of sharing and providing information related to new technology. The TWINTIER series was highly evaluated in NETIS as a technology expected to produce stable results. The series was registered as "VE Evaluation" in December 2020 (NETIS Registration Number: KT-180090-VE). Furthermore, the TWINTIER series has been recognized as an outstanding technology and selected for the Utilization Promotion Technology (New Technology Utilization Evaluation Conference (Chubu Regional Development Bureau)).
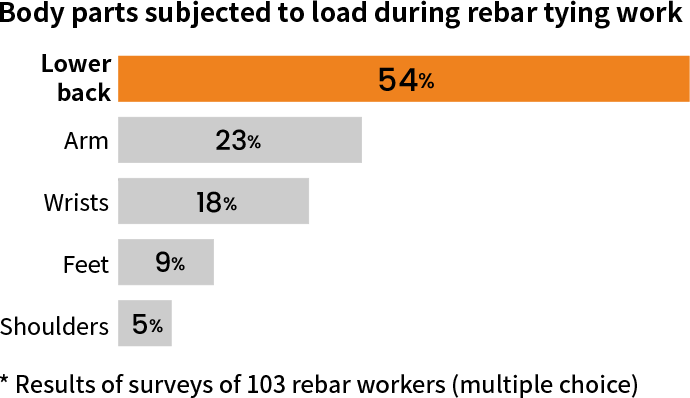
Compression force on lumbar discs | Approx. 40% reduction |
---|---|
Calories burned during work | Approx. 85% reduction |
Working hours | Approx. 40% reduction |
"Rentool" tool subscription/rental service
MAX's subsidiary Rentool Co., Ltd. operates a tool subscription/rental service covering Tokyo and six neighboring prefectures.
The system originated from an internal business contest, and allows users to use tools on either a subscription or rental basis in accordance with their own circumstances.
In recent years, the construction industry has been experiencing a decline in the number of young carpenters.
Rentool offers a long-term subscription service to address needs like "wanting to have required tools up front" as a way of lowering the barrier to entry for young people becoming carpenters by holding down the initial cost of purchasing tools.
A short-term rental service is also available to address needs like "tools needed only at this jobsite" and "wanting to give new products a try." Providing opportunities to use a variety of tools also helps to enhance the skills of young carpenters.
Our aim is to resolve the social issues of "a high percentage of young carpenters leaving their jobs" and "an insufficient number of new carpenters," while also "invigorating the housing market and achieving a society that accelerates superior community-building."
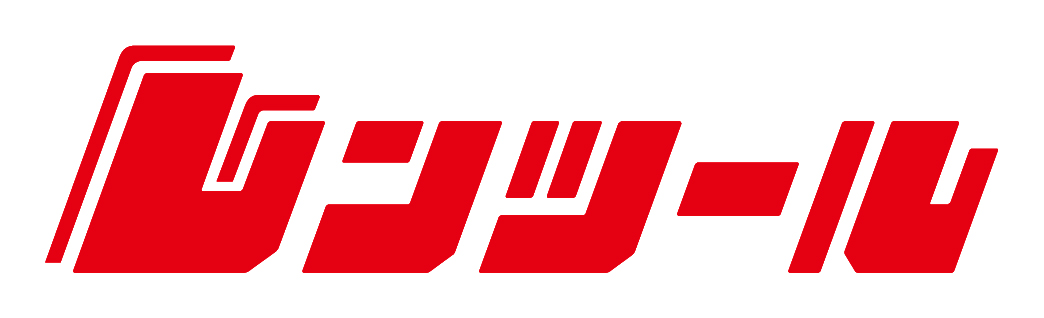
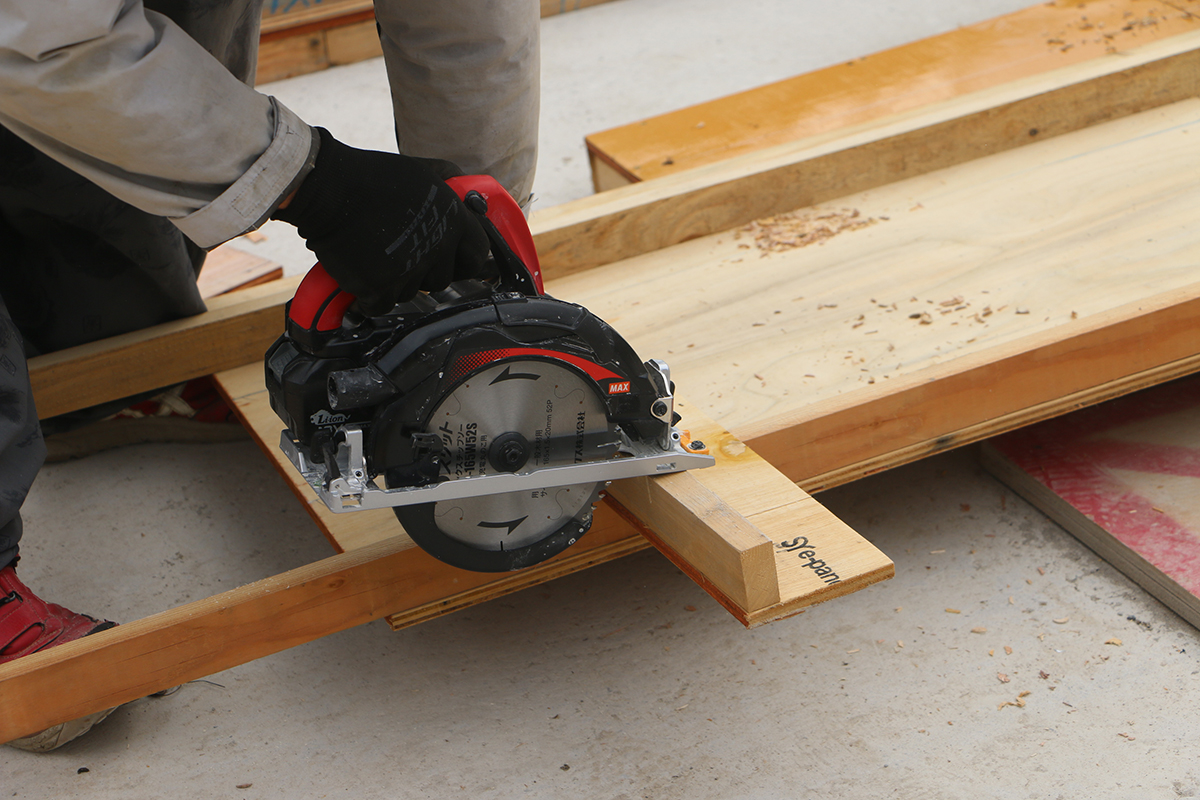
Promotion of environmentally friendly initiatives
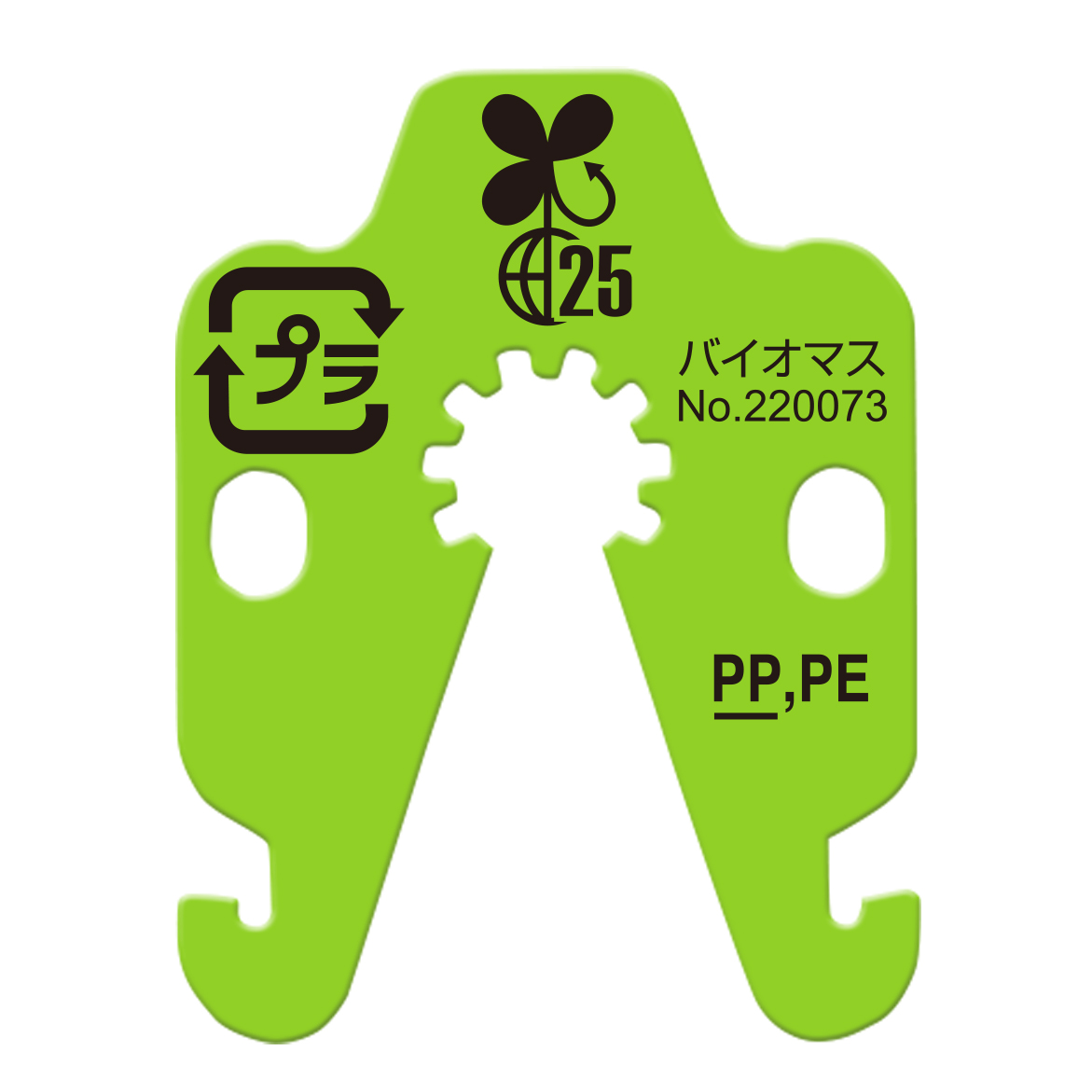
Use of biomass materials
We have developed "Biomass Plastic Staple" and "Biomass CONI-CLIP" containing biomass materials as dedicated consumables for our "AIR PACKNER" and "CONI-CLIPPER" bag closing tools. Previously, we used petroleum-derived plastics, but we are now working to reduce our environmental impact by incorporating a mix of plant-derived biomass material. Biomass plastic containing biomass material has been drawing attention for its ability to curb emissions of greenhouse gases compared with petroleum-derived plastics.
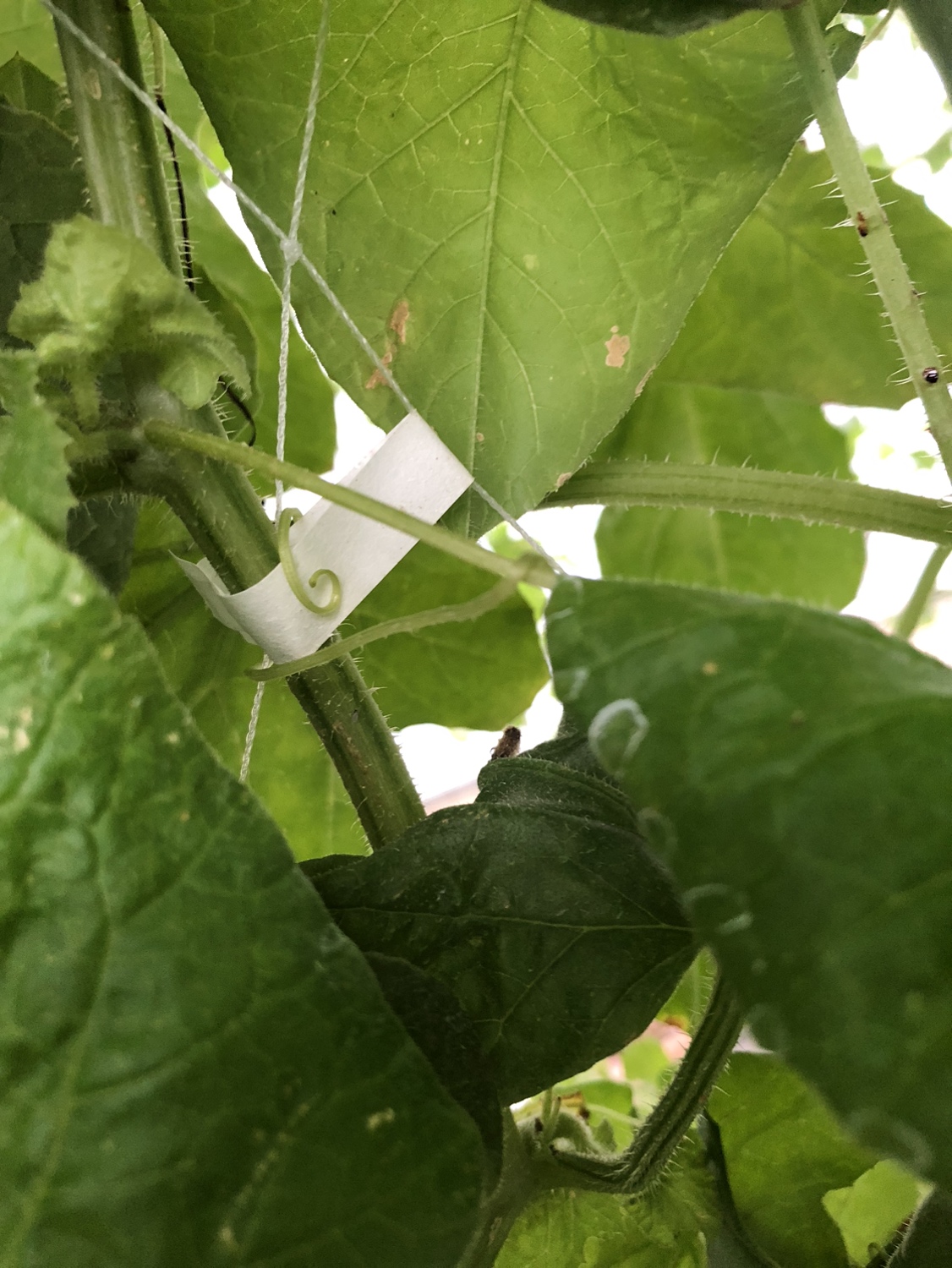
Paper tape that decomposes in soil
We have developed paper tape that decomposes in soil in about three months as a dedicated consumable for our "TAPENER" mechanical tape binding tool. In the past, used tape has been incinerated together with discarded branches and stems, but an increasing number of regions have placed restrictions on incineration. In these cases, the tape is either buried or collected, but there has been an increasing resistance to burying among producers, while collection is problematic because of the required effort. Tape made from paper material will decompose in soil in about three months, reducing environmental impact and resolving these issues.
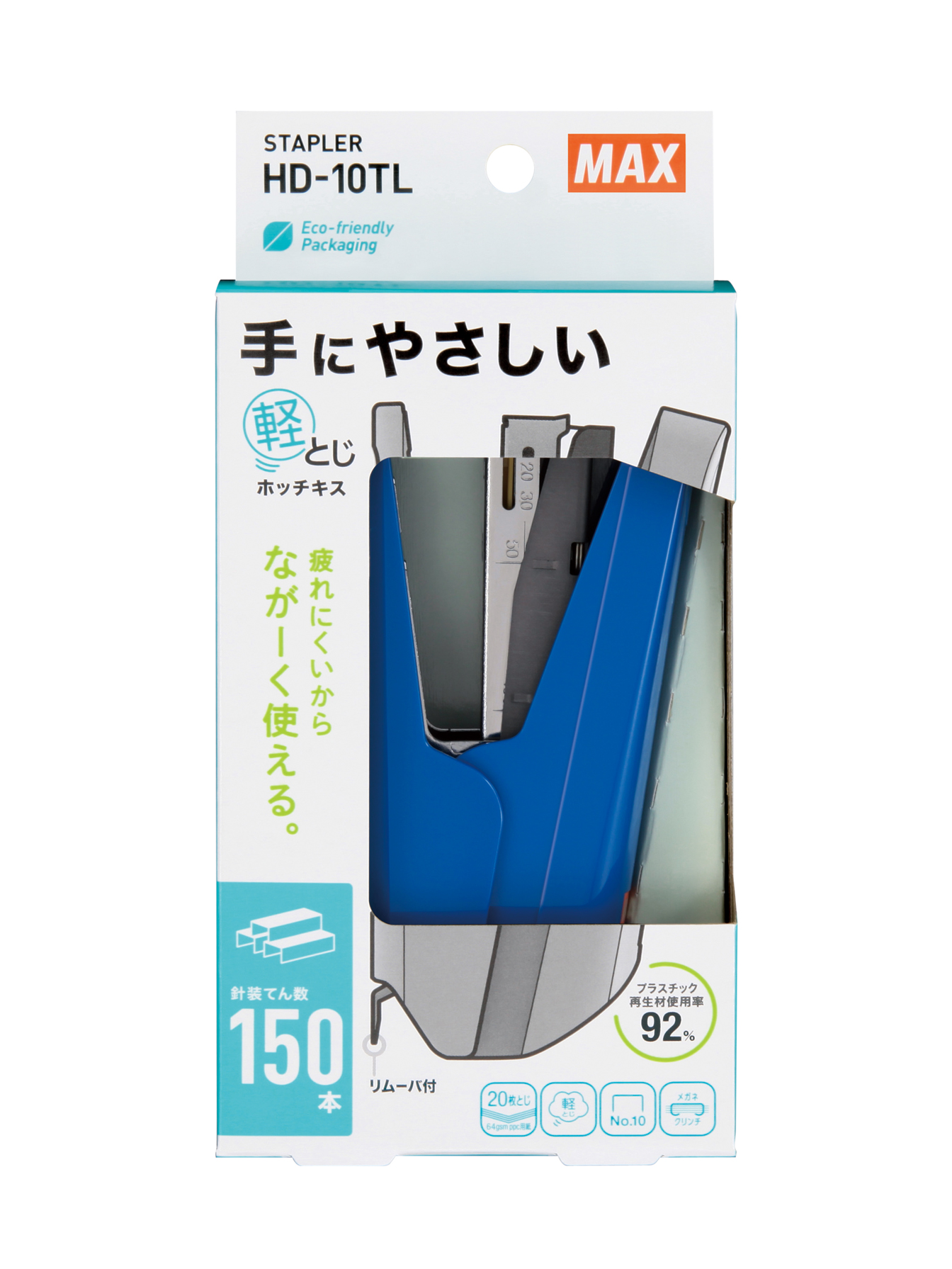
Switching from plastic packaging to cardboard
We launched a sustainable stationery series called "Re:max." With this series, we will contribute to the environment by developing stationery that moves away from plastic items and packaging and uses environmentally friendly materials. Our first initiative is the renewal of the "HD-10TL" stapler, changing from plastic packaging to cardboard.
Environmental considerations and initiatives to revitalize local industries
MAX has developed the "Re:max" environmentally friendly stationery series that features reduced use of plastic. The third round of the series is a stapler that uses "leather" and "wood" as materials for the main unit's cover, and was jointly planned with the companies that supply the wood and leather scraps that are used for the material. The scraps that are left over from the manufacturing of bags and furniture are upcycled, and the product is produced completely by hand using the skilled techniques of artisans. In addition to the environmental aspect of utilizing these scraps for which previously there was little use, we also believe that this joint endeavor is leading to the revitalization of our partners' local industries.
Leather stapler
This product was jointly planned with Maison Def, which is located in Toyooka City, Hyogo Prefecture. The product came about through the alignment of MAX's desire to revitalize a local industry using environmentally friendly materials and Maison Def's desire to use materials left over from the bag-making processes to create new value. The product uses KOBE LEATHER® and taurillon leather (made from a young bull), and comes in innovative, stylish colors. The rivets used in the structural material and as ornamentation accent the overall design.
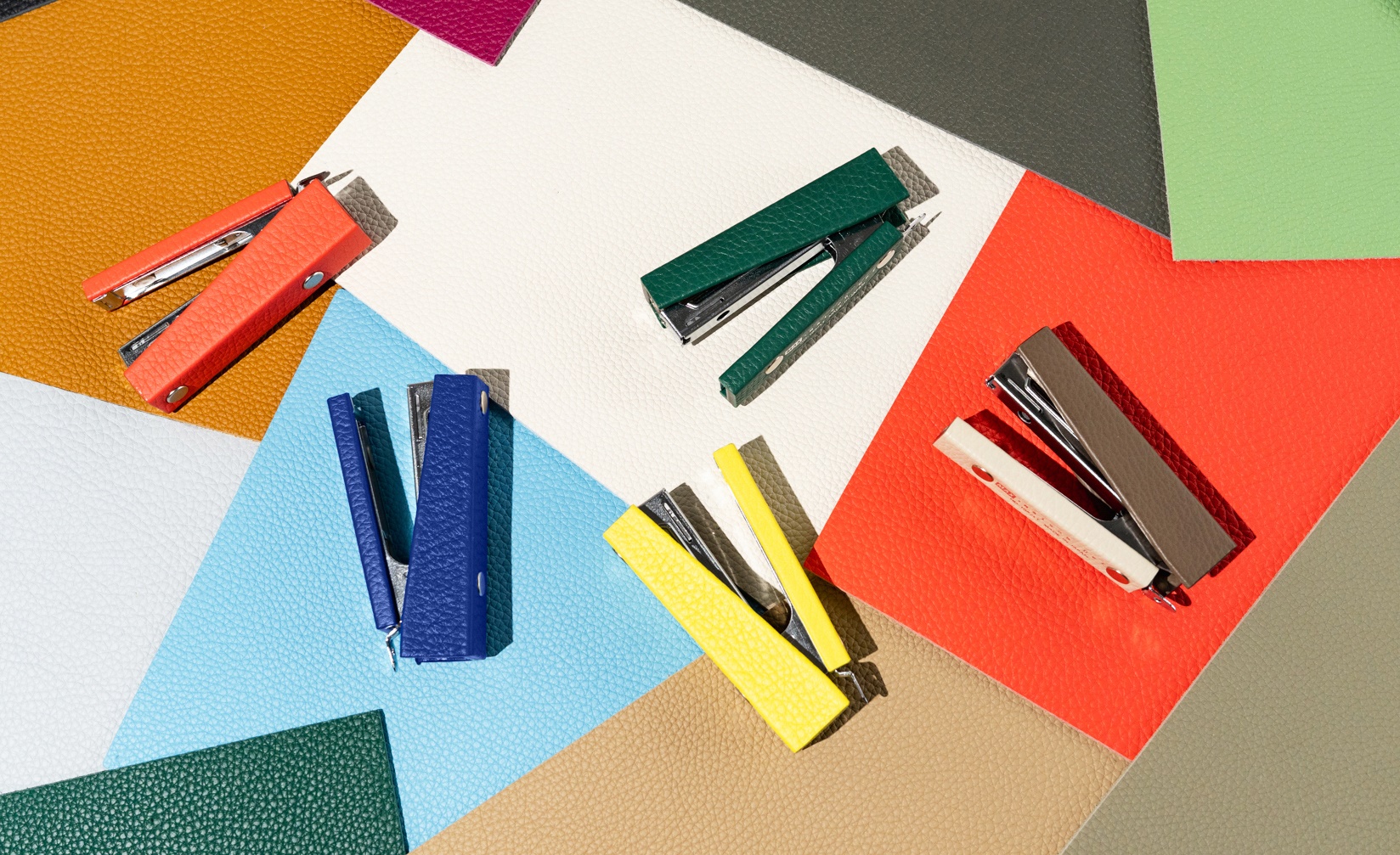
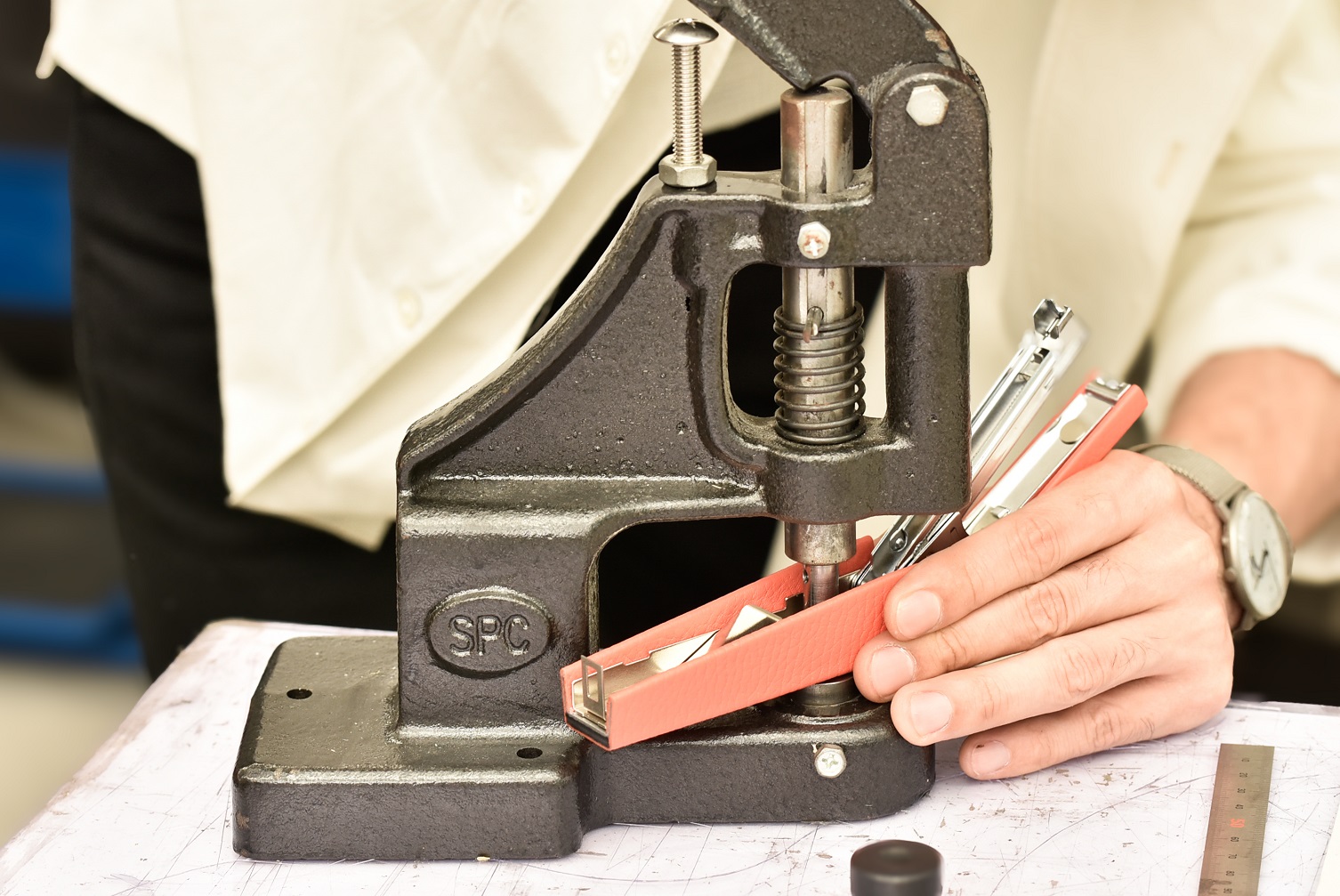
Wooden stapler
This product was jointly planned with furniture&lifestyle factory and kochi, which are located in Takayama City, Gifu Prefecture, an area with a vibrant woodworking industry. The wood materials provided by furniture&lifestyle factory come from broad-leaved trees in the forests of nearby Hida Takayama, with scraps left over from furniture manufacturing upcycled into staplers. The artisans at kochi carefully make each item by hand. Four types of wood are currently being used: mountain cherry, chestnut, walnut, and beech.
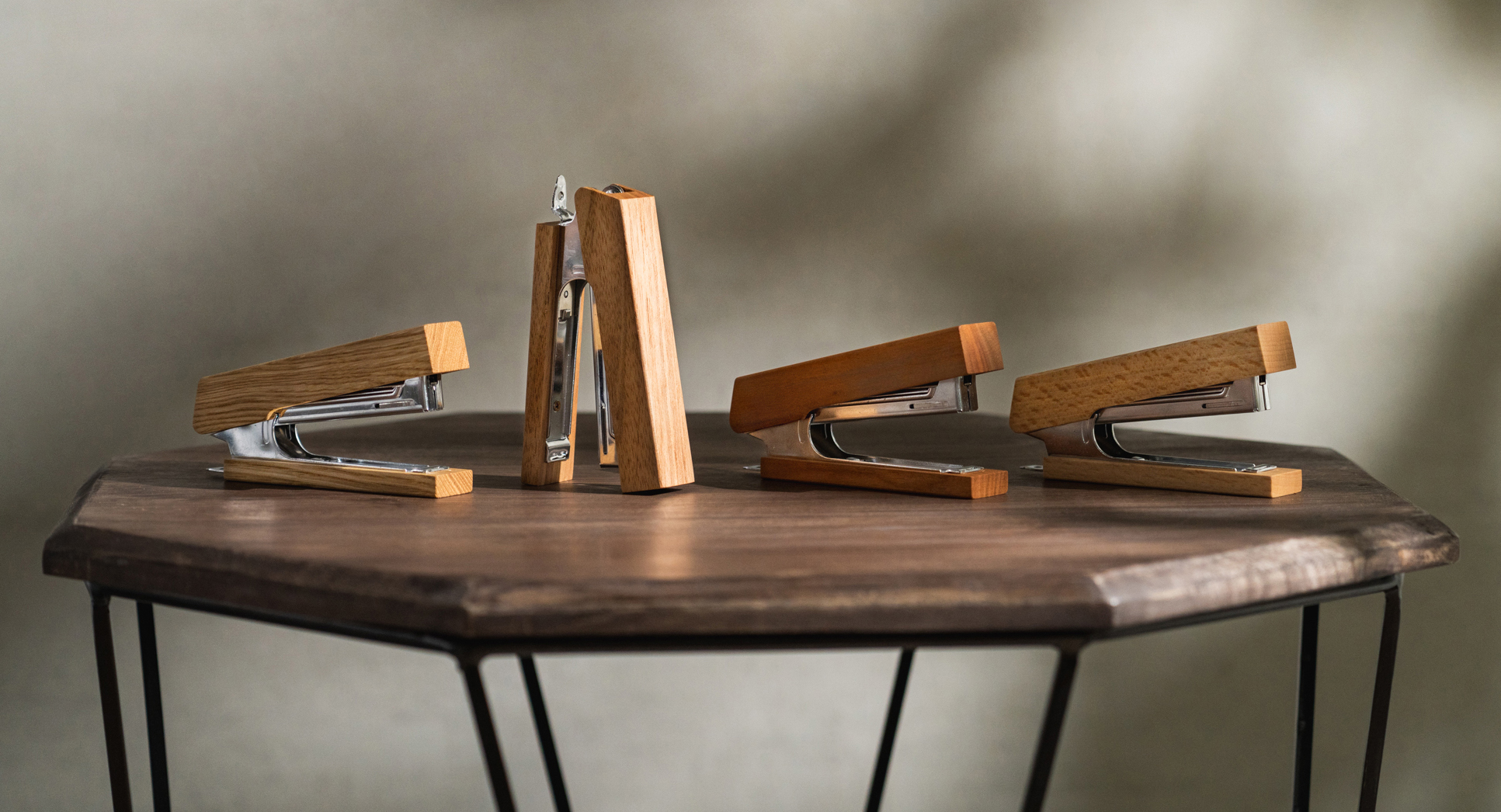
The contest for safety signs and awareness training
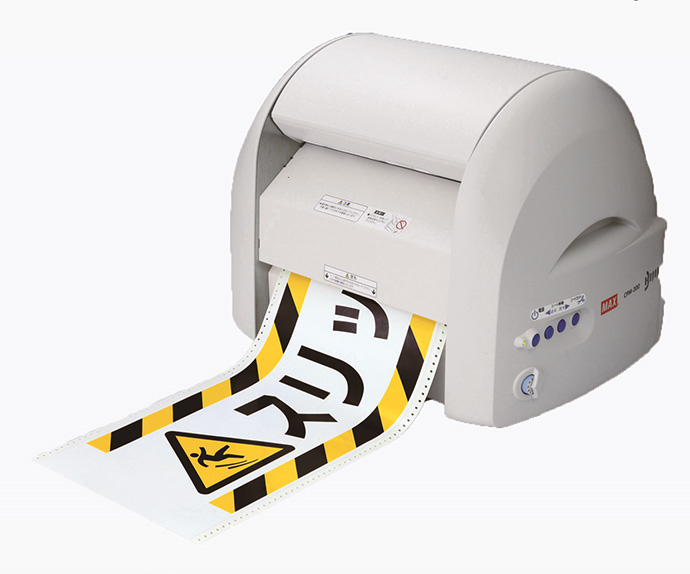
Every year, in Japan, MAX holds a "contest for safety signs and safety awareness training", in which participants use our sign & label printing machine "Bepop" to reduce labor accidents. During the contest, participants work together to check dangerous places and create signs to warn about such places. We believe that by having participants do so, they can learn how to solve dangers and issues in their workplace together. The fundamental reason for holding this contest is to encourage people to conduct "voluntary" improvement activities, and we believe this reason shares some similarities with our fundamental management policy, which is "to become a group in which everyone can grow together by creating a lively and fun atmosphere." MAX will continue contributing to reducing labor accidents by "creating a workplace with a positive and lively atomosphere."
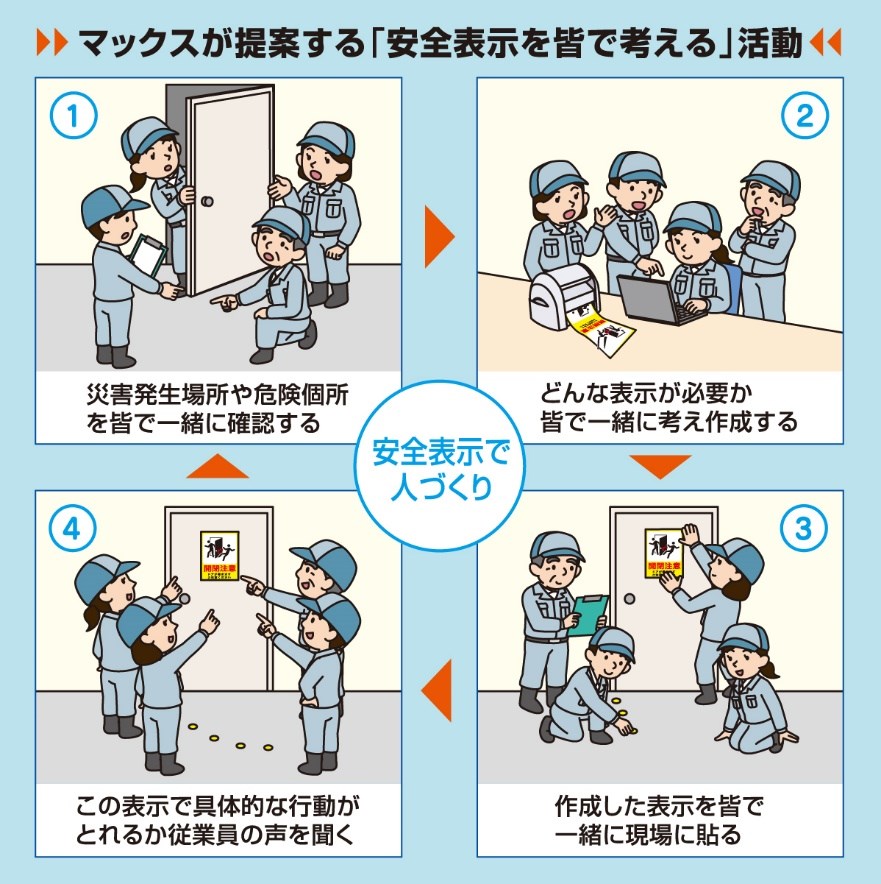
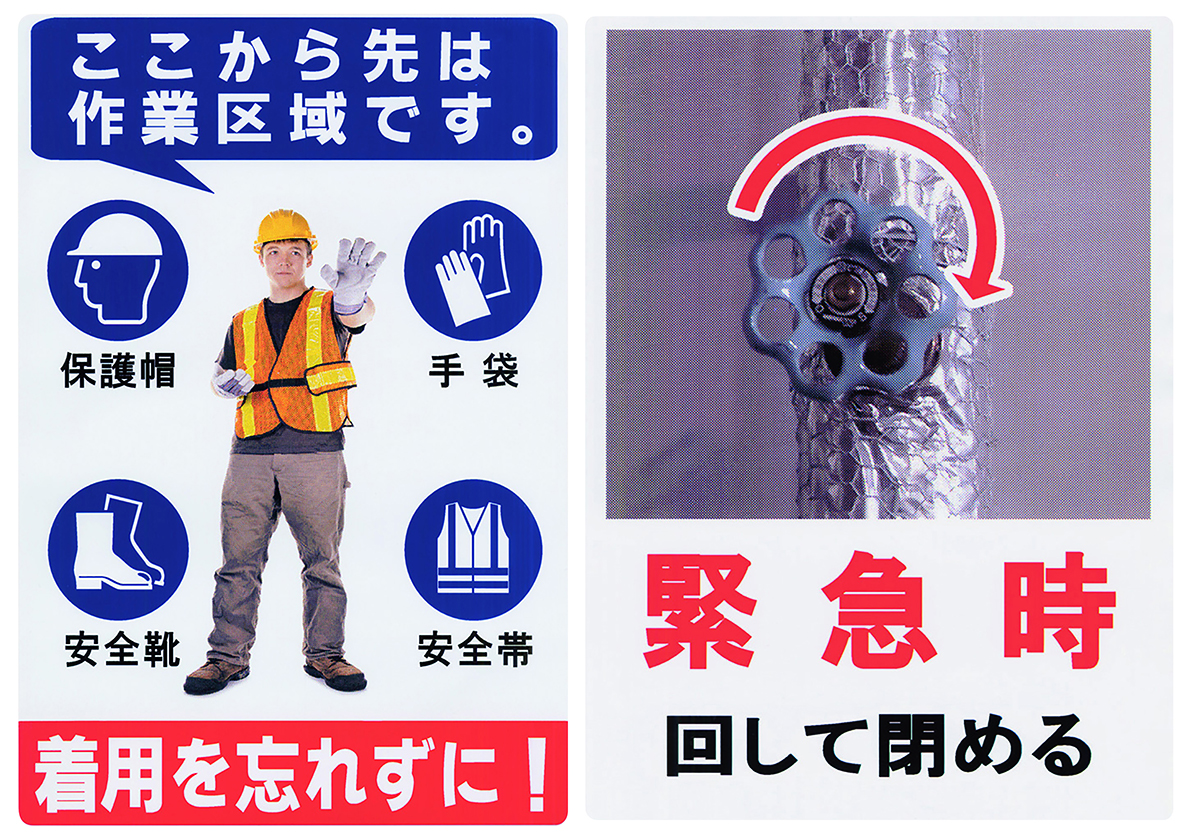
"DRYFAN" a heater-ventilator-dryer for bathrooms
Since its sales started in 1985, more than 8.1 million units (total number of shipments) have been used by our customers. "DRYFAN" has maintained its No. 1 share* in the market because we have prepared a varied lineup for various usage purposes, such as DRYFAN for apartments, for condominiums and for stand-alone houses, as well as DRYFAN with plasma-cluster technology*. It contributes to reducing various risks, such as sick house syndrome that can occur in air-tight houses.
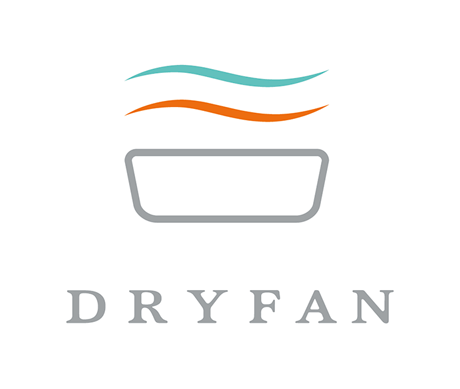
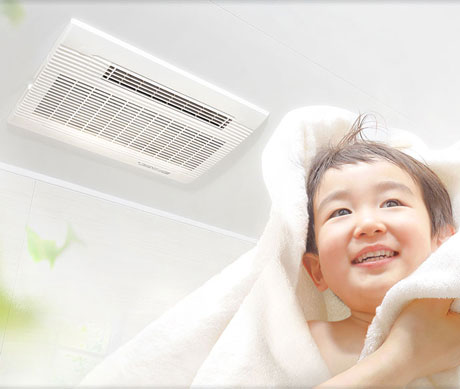
- *Housing Equipments and Building Materials Market Trend Data Handbook 2024,
Electric Heater/Dryers for Bathrooms, Market Share by Manufacturers (FY2024 Forecast)
According to the market research by Fuji Keizai Co., Ltd.(as of June 2024) - *"Plasmacluster" and "Device of a cluster of grapes" are trademarks of Sharp Corporation.
Contributing to society through wheelchairs
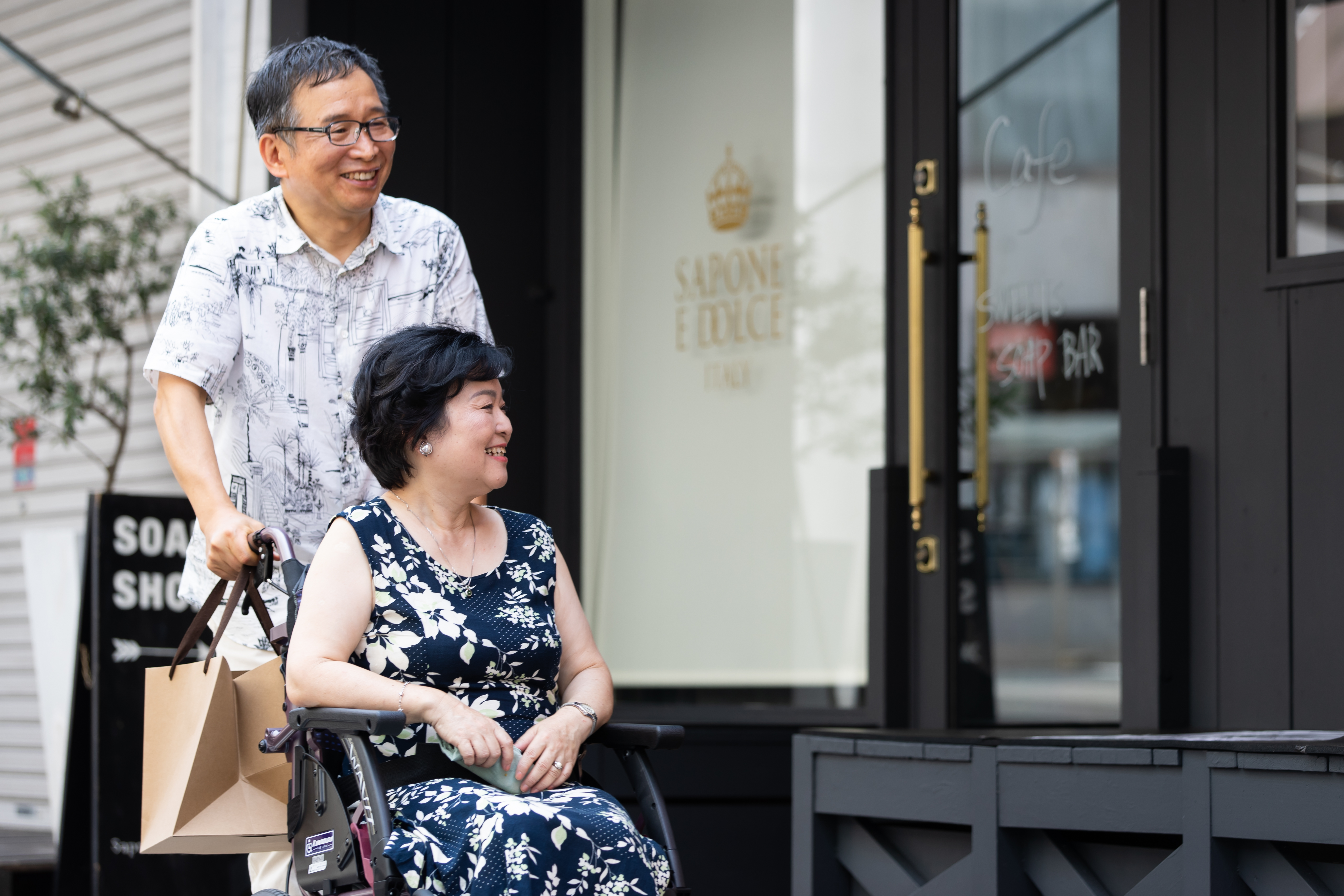
Since its founding in 1995, the MAX Group company Kawamura Cycle Co., Ltd. has been developing wheelchairs that match the lifestyles of caregivers and users to contribute to the creation of comfortable living. Wheelchairs are not simply a convenience, they are welfare products that are indispensable to the lives of the people who use them. As a manufacturer handling welfare products, Kawamura Cycle is proactively working to contribute to society with the hope of providing what help it can to people who need it. Kawamura Cycle will continue to strive to support people's full lives through the development, manufacturing, and sales of wheelchairs.
Workplace experience at special support schools
In March 2024, we hosted a workplace experience program for a special support school. The school was looking for companies that students could visit in areas where they lived, and asked Kawamura Cycle to participate.
The company was a bit nervous as it was its first time participating in the program, but it hosted one student who spent a week experiencing the workplace.
The experience began with a tour of Kawamura Cycle to familiarize the student with the company, followed by the student experiencing various clerical operations and concluding with a discussion with young employees.
In addition to experiencing actual operations, the student was encouraged to express "greetings," which is one of the most important things for a working adult.
Having the student proactively engage in greetings and experience the workplace also gave stimulation to the employees, while at the same time reminding them that their work contributes to society.
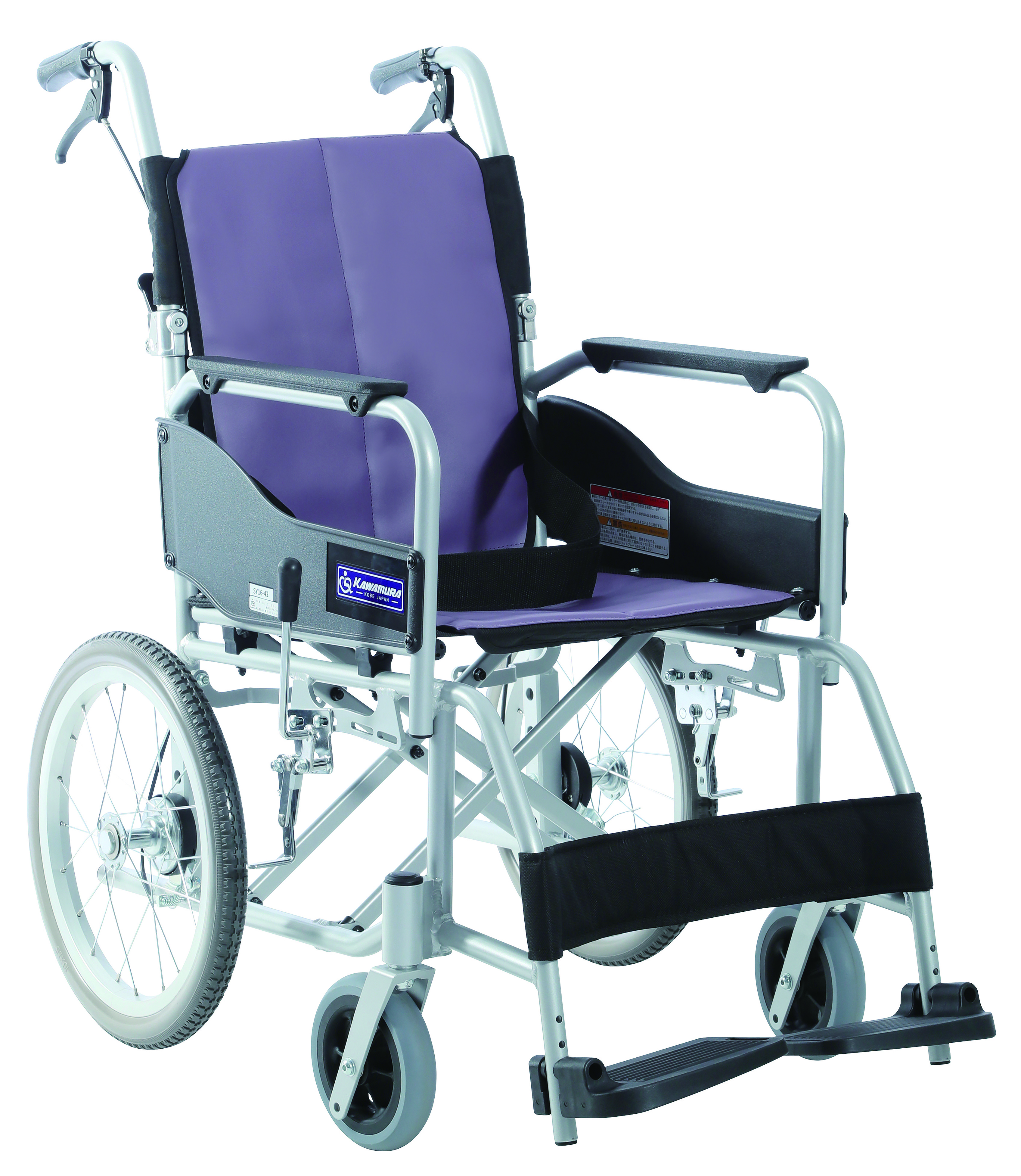
Wheelchair donations
In March 2023, we provided 10 new wheelchairs through a volunteer organization that is sending wheelchairs to Ukraine following that country's invasion by Russia. We continue to support this effort with packaging materials that are used to send wheelchairs donated from around Japan. We hope that through these various support activities, Kawamura Cycle's wheelchairs will prove useful for even more people.
Contributing to local communities
We outsource operations for boxing staples and bagging wheelchair instruction manuals as a way to support employment for people with disabilities.
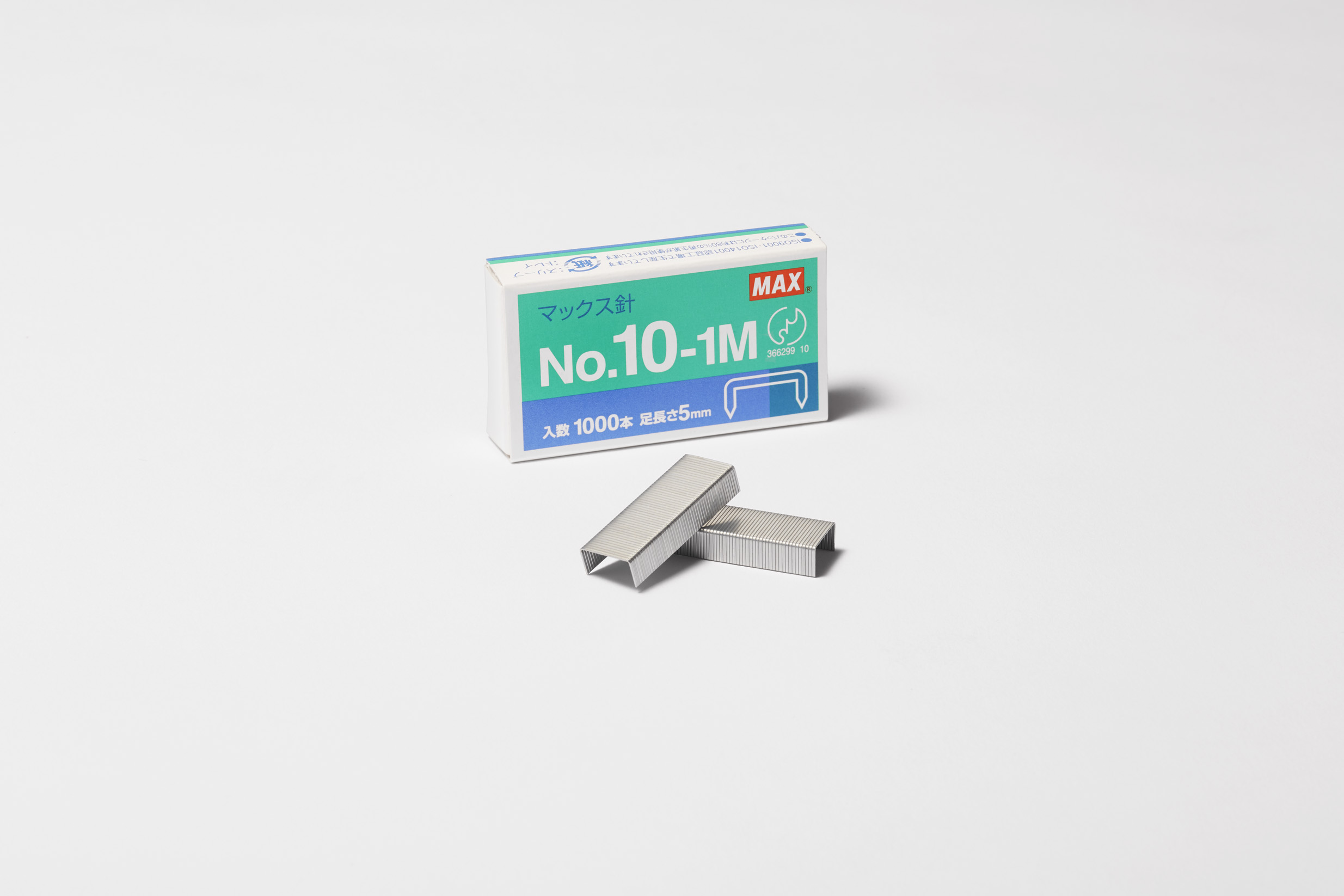