Our activities for reducing the environmental burden
Reducing environmental burden by installing solar power system
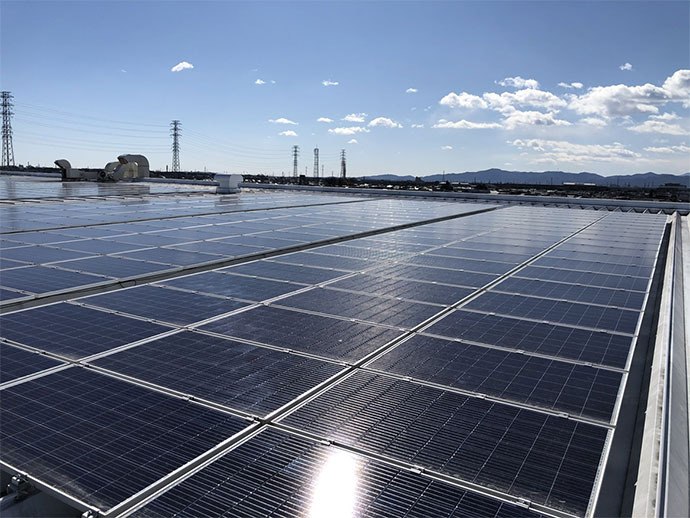
In 2021, we installed solar power system at our newly built Yoshii Logistics Warehouse, reducing CO2 emissions by 110 tons per year, and we are expanding the use of renewable energy throughout the Group, including the introduction of a solar power system at our third plant in Thailand, which started operation in March 2023.
Changing to LED Lights for Domestic Offices
The MAX Group is actively promoting the use of LED lighting. LED lighting accounts for about 75% of the total number of light bulbs in our domestic offices. Moving forward, we will continue to promote LED lighting and strive to decrease CO2 emissions by reducing power consumption.
Introduction of Hybrid Vehicles
Hybrid vehicles comprise approximately 50% of all vehicles at the MAX Group's domestic offices. In the future, we will work to reduce CO2 emissions by switching to hybrid vehicles and electric vehicles as we replace vehicles.
Promotion of environmentally friendly initiatives
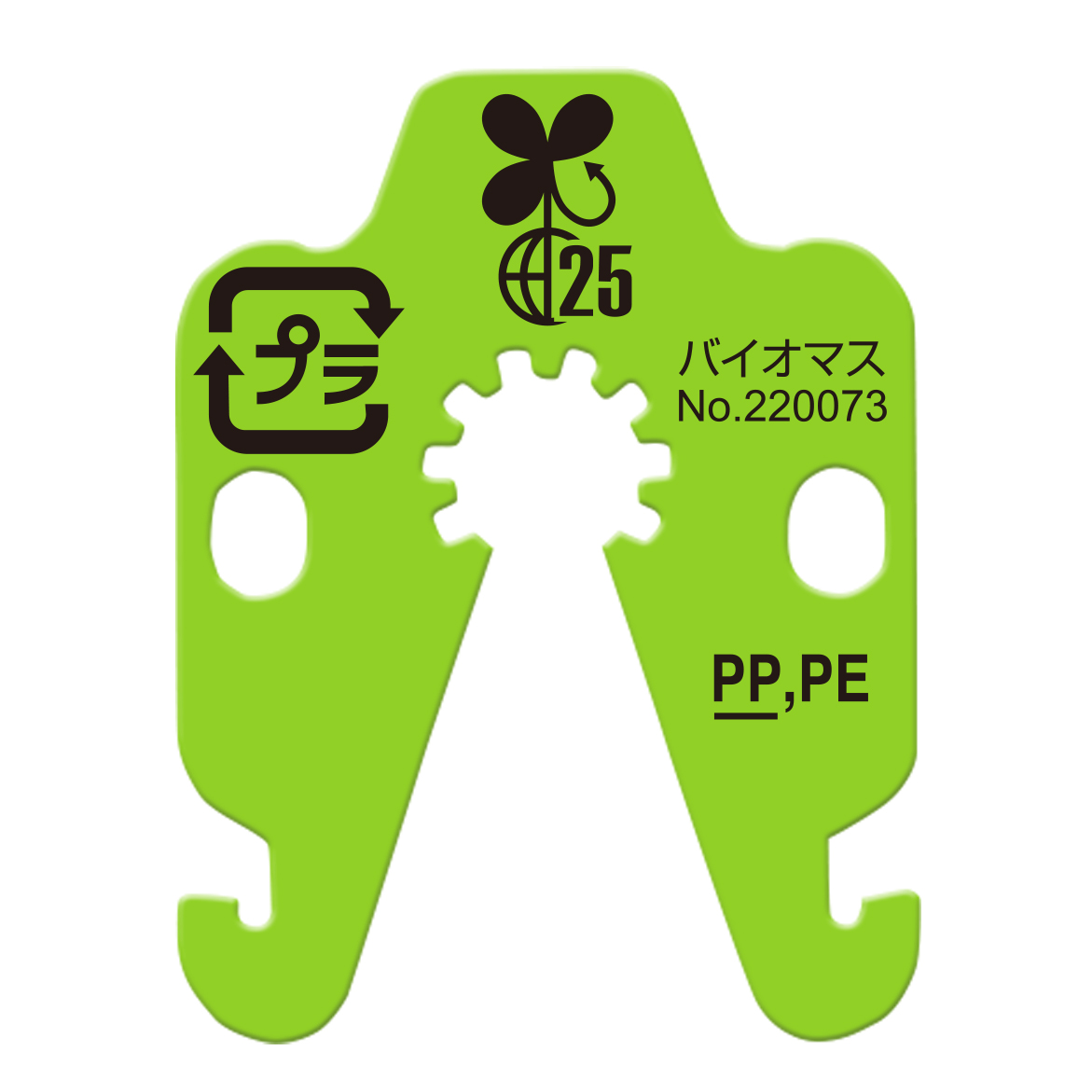
Use of biomass materials
We have developed “Biomass Plastic Staple” and “Biomass CONI-CLIP” containing biomass materials as dedicated consumables for our “AIR PACKNER” and “CONI-CLIPPER” bag closing tools. Previously, we used petroleum-derived plastics, but we are now working to reduce our environmental impact by incorporating a mix of plant-derived biomass material. Biomass plastic containing biomass material has been drawing attention for its ability to curb emissions of greenhouse gases compared with petroleum-derived plastics.
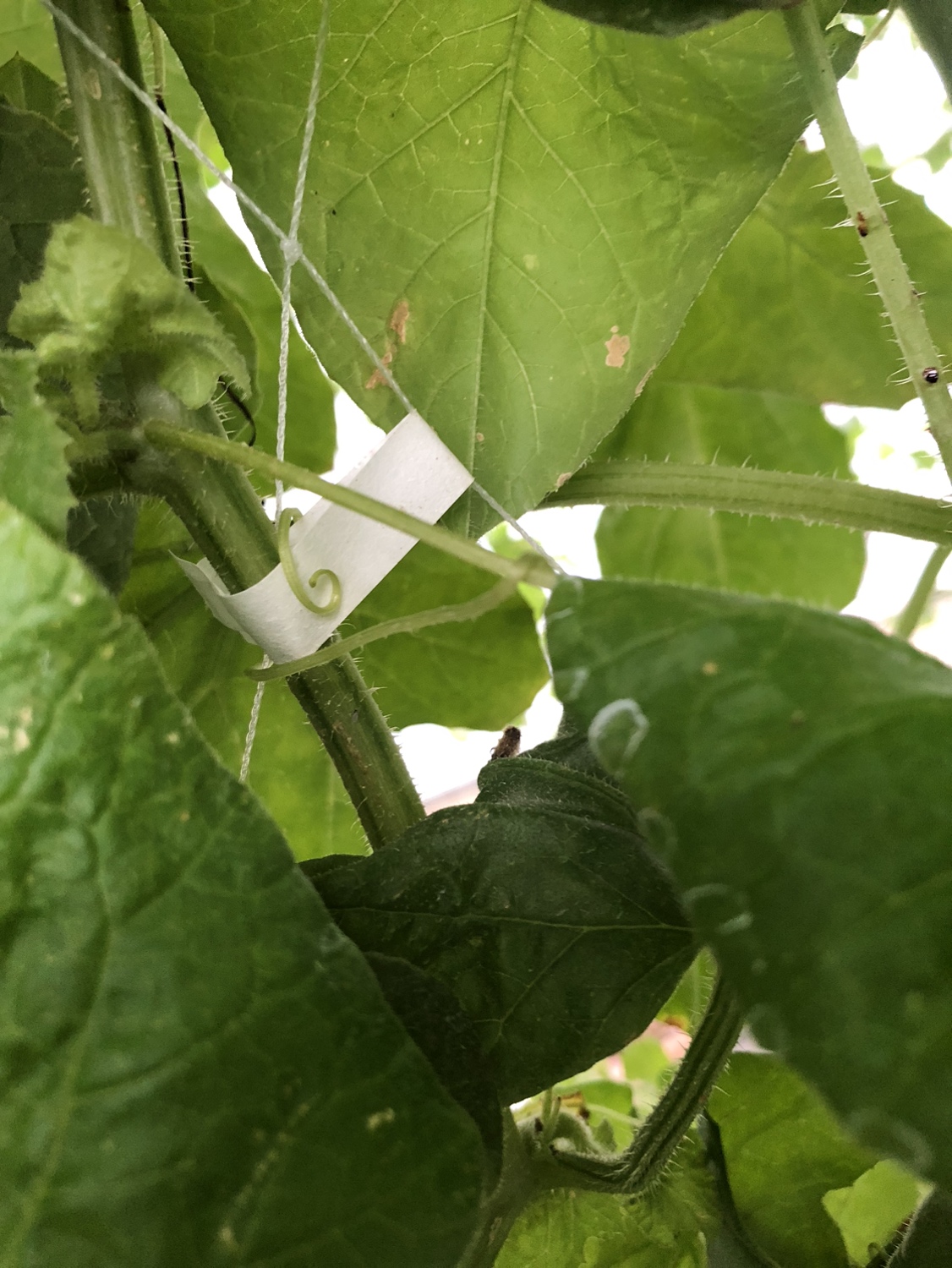
Paper tape that decomposes in soil
We have developed paper tape that decomposes in soil in about three months as a dedicated consumable for our “TAPENER” mechanical tape binding tool. In the past, used tape has been incinerated together with discarded branches and stems, but an increasing number of regions have placed restrictions on incineration. In these cases, the tape is either buried or collected, but there has been an increasing resistance to burying among producers, while collection is problematic because of the required effort. Tape made from paper material will decompose in soil in about three months, reducing environmental impact and resolving these issues.
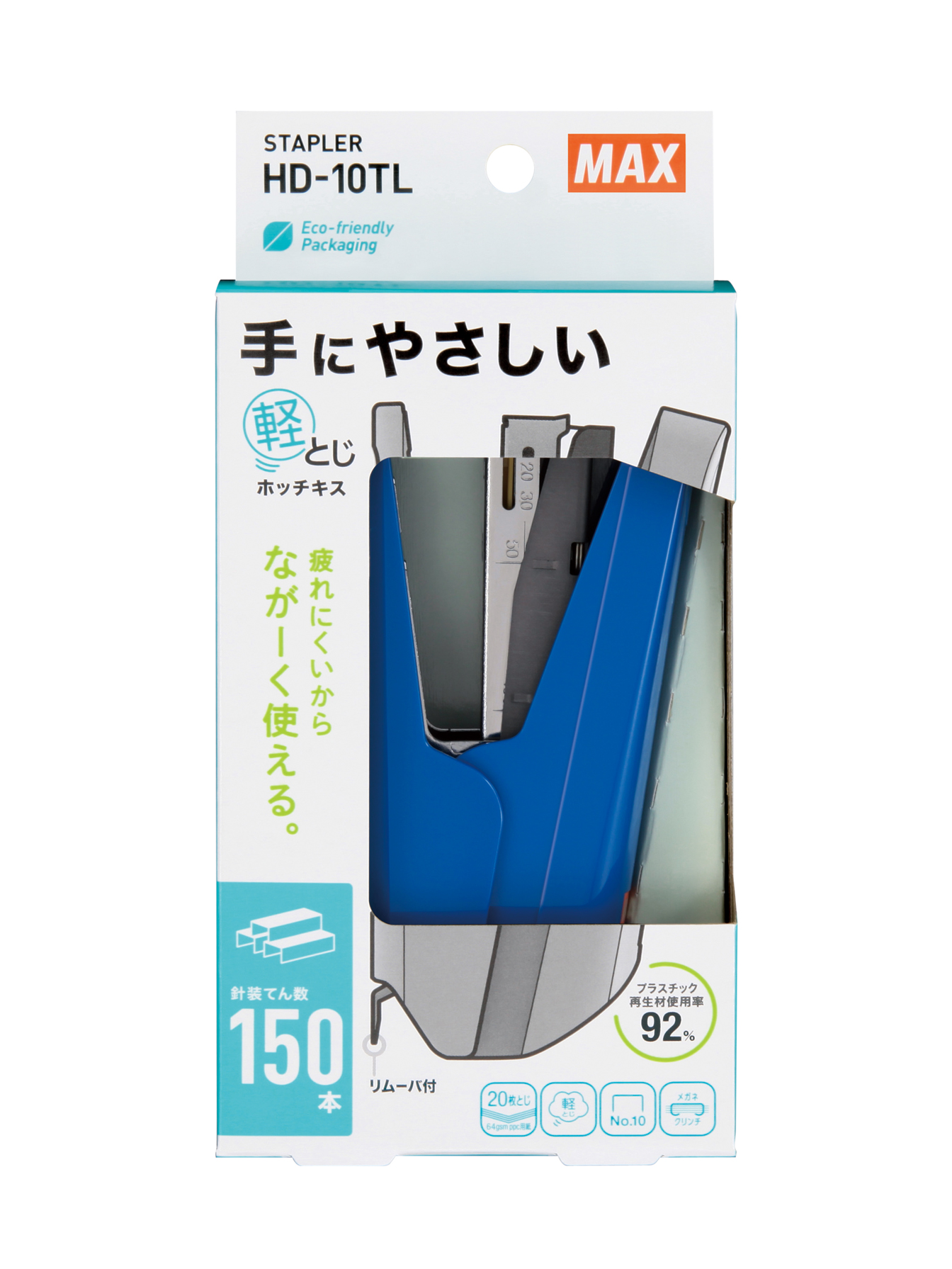
Switching from plastic packaging to cardboard
We launched a sustainable stationery series called “Re:max.” With this series, we will contribute to the environment by developing stationery that moves away from plastic items and packaging and uses environmentally friendly materials. Our first initiative is the renewal of the “HD-10TL” stapler, changing from plastic packaging to cardboard.
Energy conservation
The result was 101.5% against the fiscal 2023 target of curbing energy consumption per basic unit to 99.0% or less compared to that of the previous fiscal year.
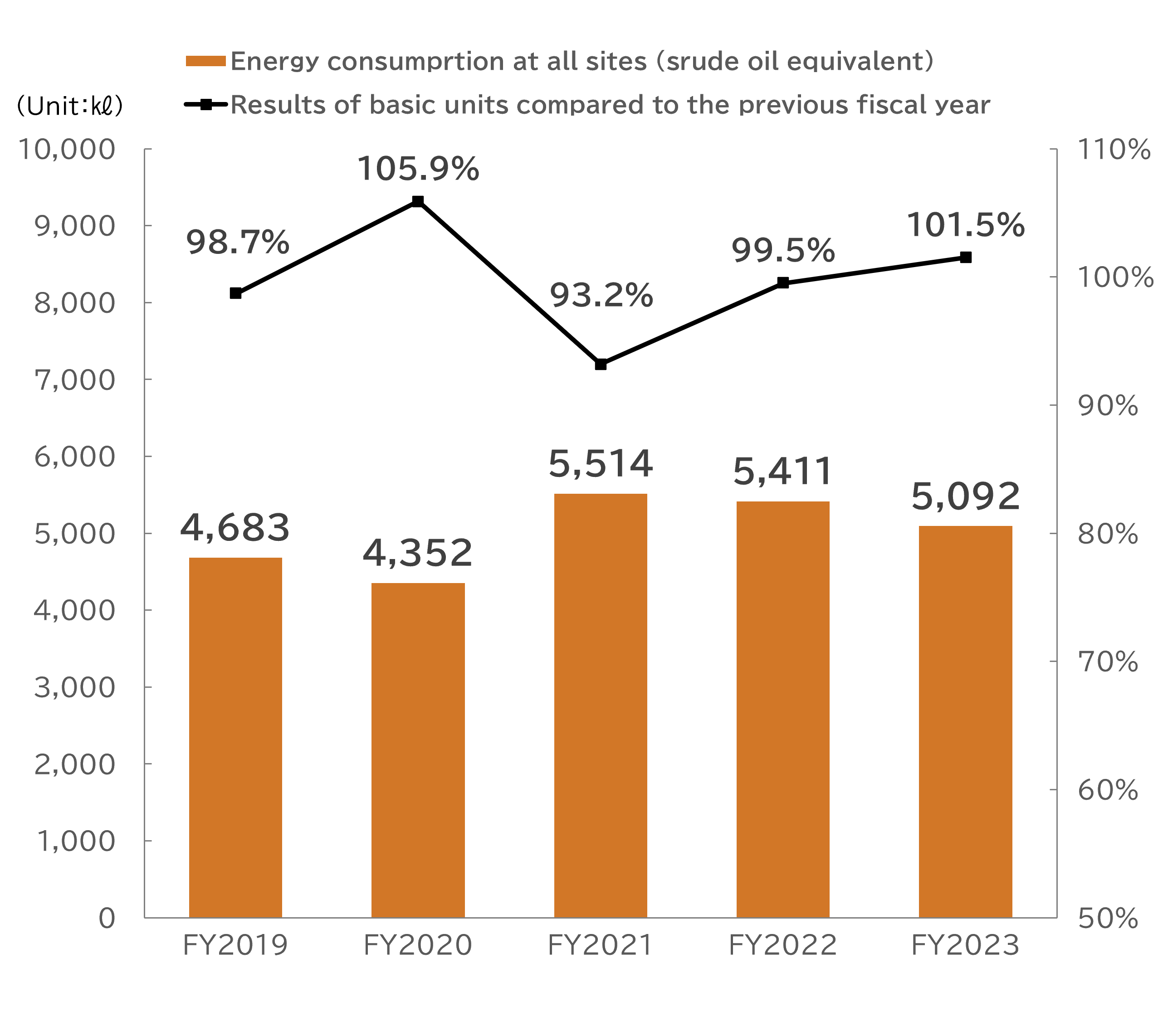
Resource Saving / Recycling
The result was 109.2%, meeting the fiscal 2023 target of curbing total emissions per basic unit to 99.0% or less compared to that of the previous fiscal year.
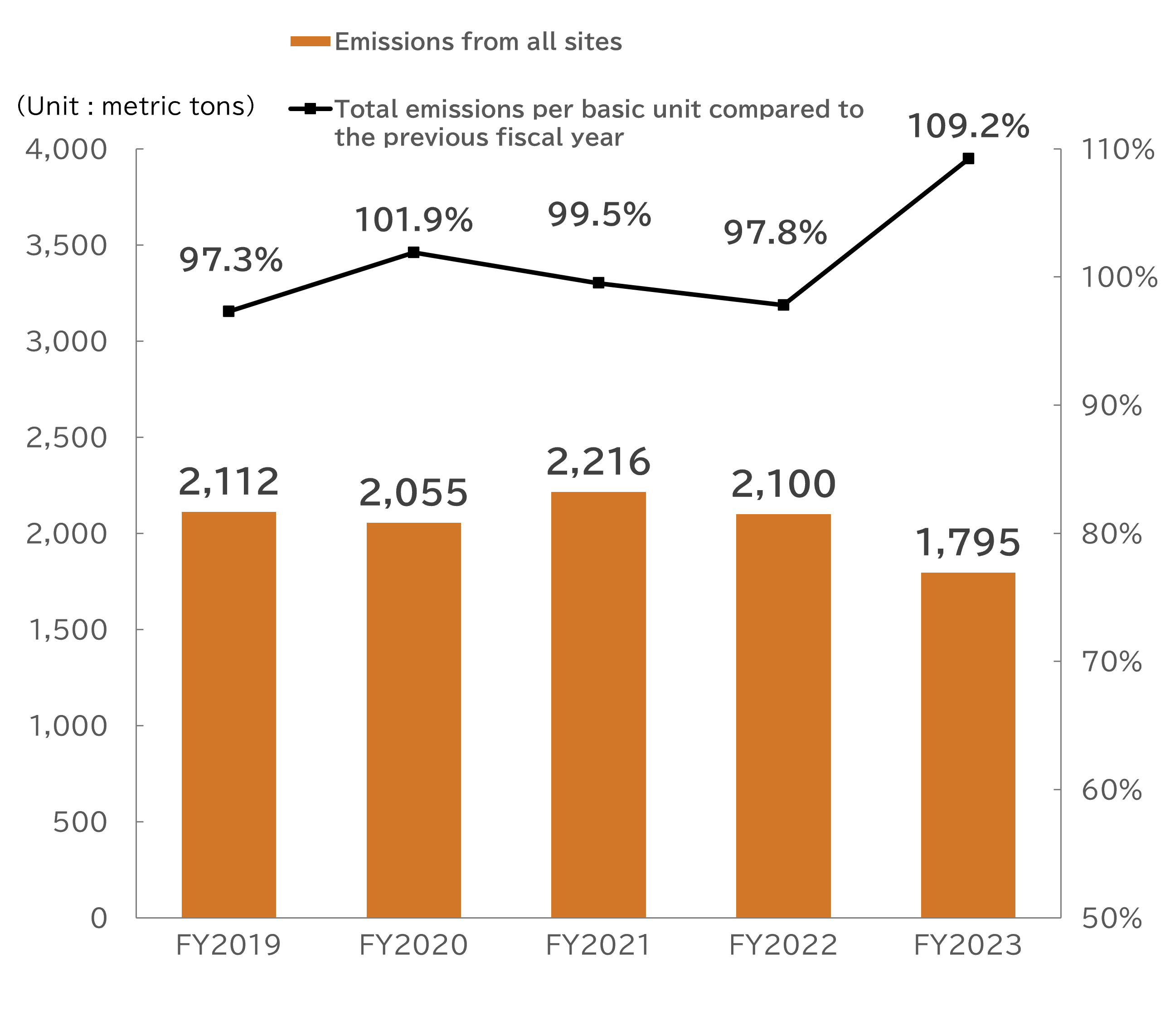
Recycling Rate
The result was 92.7% against the fiscal 2023 target of a recycling rate of 94.6% or more.

Emissions of industrial waste from plastic-using products, etc.
In FY2023, we reduced emissions of industrial waste from plastic-used products by approximately 4.4% from the previous year.
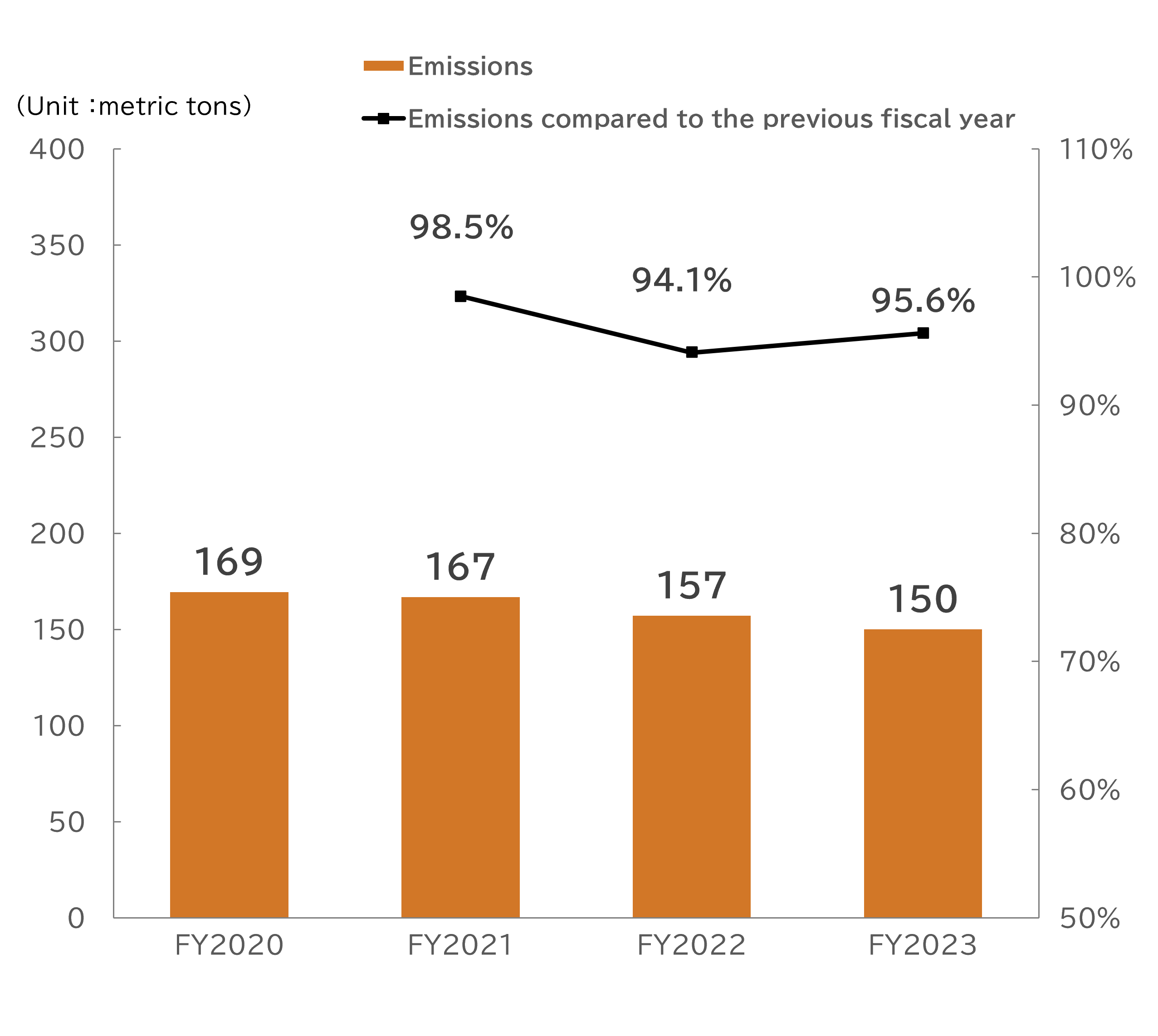
Substances Subject to the PRTR Law
The handling, transfer, and emission amount of substances at MAX subject to the PRTR Law (Class 1 Designated Chemical Substances) are as follows.
Site Name[Notification Date] | Chemical Substance Name | Handling Amount (kg) |
Emissions Amount (kg) |
Transfer Amount (kg) |
Emission Details | Transfer Details | |
---|---|---|---|---|---|---|---|
Waste Disposal Method | Types of Waste | ||||||
Tamamura(5) | Ethylbenzene | 1,278 | 980 | 49 | Atmosphere | Incineration/melting | Sludge, waste oil |
Xylene | 2,830 | 2,700 | 150 | Atmosphere | Incineration/melting | Sludge, waste oil | |
Vinyl acetate | 1,554 | 1,200 | 340 | Atmosphere | Incineration/melting | Waste oil, waste plastics | |
Toluene | 12,337 | 8,900 | 2,600 | Atmosphere | Incineration/melting | Sludge, waste oil, waste plastics | |
Formaldehyde | 640 | 0 | 0 | - | Incineration/melting | Sludge | |
Fujioka(6) | Zinc water-soluble compound | 50,000 | 220 | 0 | Public water area | - | - |
Ethylbenzene | 1,980 | 580 | 1,400 | Atmosphere | Others | Waste oil | |
Xylene | 2,470 | 770 | 1,700 | Atmosphere | Others | Waste oil | |
Toluene | 7,300 | 5,500 | 1,800 | Atmosphere | Others | Waste oil | |
Normal hexane | 6,400 | 3,100 | 770 | Atmosphere | Others | Waste oil | |
Methylnaphthalene | 2,300 | 12 | 0 | Atmosphere | - | - | |
Joban(2) | Toluene | 411 | 330 | 81 | Atmosphere | Incineration/melting | Waste oil |
Naphthalene (liquid) | 2.4 | 1.9 | 0.5 | Atmosphere | Incineration/melting | Waste oil |
Conservation of Water Resources
Each factory is located in a region where the risk of drought is low. City water (tap water) and groundwater are used as appropriate depending on the situation in each region.
None of MAX's production processes use a large amount of water. Instead, water is used for limited purposes such as indirect cooling of the plating process in the production of consumables such as staples and wires for rebar tying tools at the Fujioka Factory. Wastewater is properly treated and then discharged to public water areas. Moreover, some of the water is reused in processes such as cooling. However, in the future, we will further improve the reuse rate and replace it with city water in consideration of risks such as restrictions on the intake of groundwater.