MAX's products History
MAX's history reflects its insistence on "making products that fully satisfy the people who use them."
We introduce the history of the birth of Japan's first compact office stapler and hand tacker, and the subsequent development of the product in response to customer voices.
1942~1950
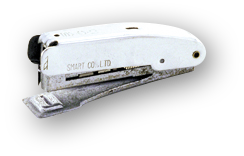
MAX has always promptly identified up-to-date needs, MAX produced Japan's first compact office stapler, hand tacker and drafting machine!
The stapler "SYC-10" and the gun tacker gained the trust of customers and established the business foundation of MAX.
- 1953
- NHK TV broadcasting begins.
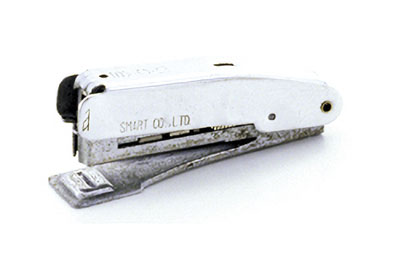
Japan's first No. 10 stapler "SYC-10" is released
- 1958
- Tokyo Tower opened.
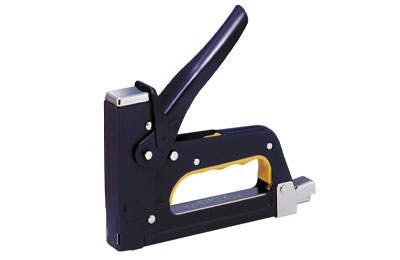
Japan's first hand tacker is released
1960~1970
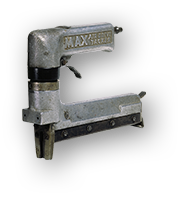
- 1960s
- Period of high growth
The development of pneumatic technology, MAX's nailers became air-powered, and the market for them was expanded to cover furniture, packaging and construction!
Naira's consumables also expanded from staples to nails, and the materials to be driven into expanded from wood to steel plates and concrete, and Naira penetrated all markets that use nails, becoming the top manufacturer of nailers in Japan in both name and reality.
- 1962
- Metropolitan Expressway No. 1 opened
- 1964
- Tokyo Olympics
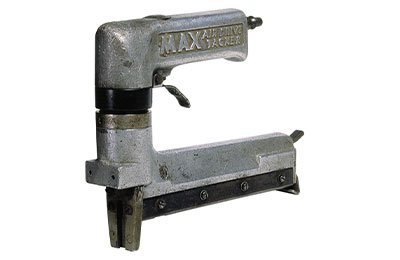
Japan's first air nailer "T2-A" is released *
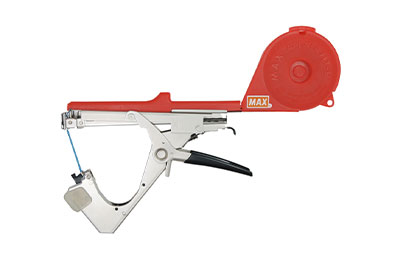
"TAPENER" mechanical tape binding tool for farming is released
- 1970
- Osaka World's Fair
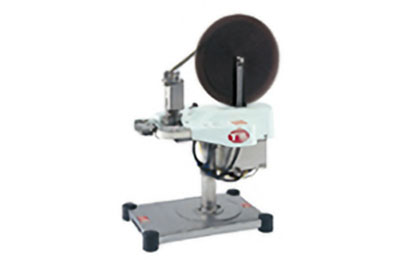
"PACKNER" bag sealer is released
- 1973
- The first oil shock
- 1974
- 2×4 construction method approved in North America
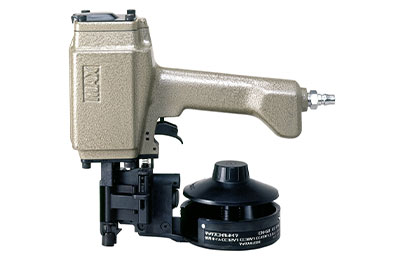
Coil nailer for wire collated nails "CN-60" is released *
- 1979
- Second oil shock
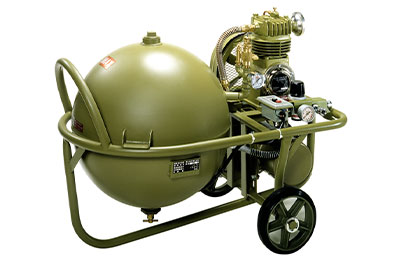
Air compressor for nailers is released *
Products with * are obsolete products.
1980~1990
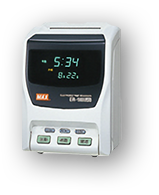
- 1982
- Joetsu Shinkansen begins service.
Electronics technologies were introduced in many fields, and MAX created new markets through the introduction of electronic technologies in office equipment such as check writers, time recorders and staplers.
MAX introduced new concept products for the next generation by uniting the technologies it had accumulated, such as the PowerLite high-pressure pneumatic nailer, a concrete reinforcing bar tying machine (RE-BAR-TIER), a built-in electronic stapler for multi-function copiers (auto stapler), and a sign & label printing machine (Bepop).
- 1985
- Science Expo Tsukuba 85
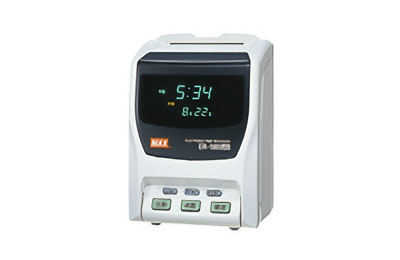
Electronic time recorder is released
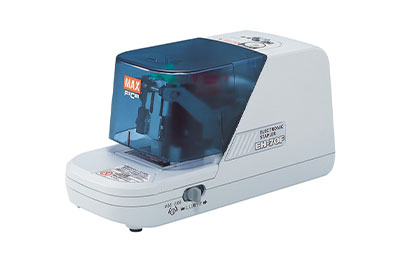
Electronic stapler is released
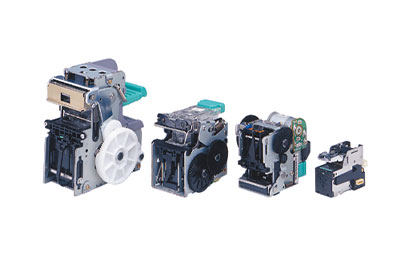
"AUTO STAPLER" a stapler for printer/copier finishers is released
- 1989
- New era begins with the start of the Heisei era.
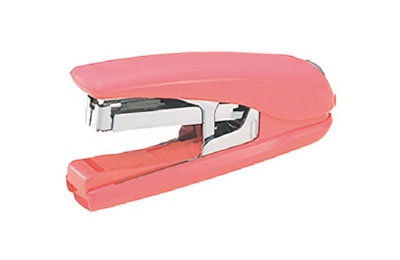
A flat clinch stapler which makes the back side of stapled sheets flat is released
- Around 1990
- Bubble economy bursts
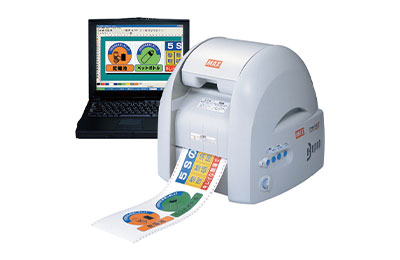
"Bepop" a sign & label printing machine is released
- 1993
- The J-League soccer tournament begins.
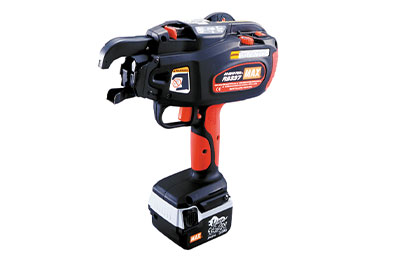
"RE-BAR-TIER" a concrete reinforcing bar tying machine is released
- 1995
- Great Hanshin-Awaji Earthquake
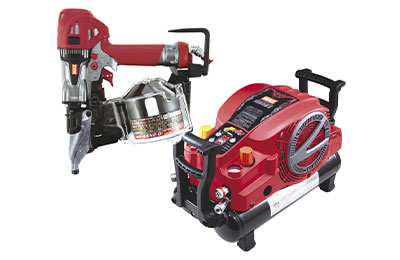
"SUPER NAILER/SUPER AIR COMPRESSOR" a high-pressure nail driving system is rereased
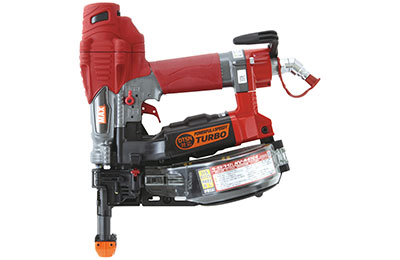
"TURBO DRIVER" a collated screw driving machine to be used on drywall is released
- 1998
- Nagano Olympics
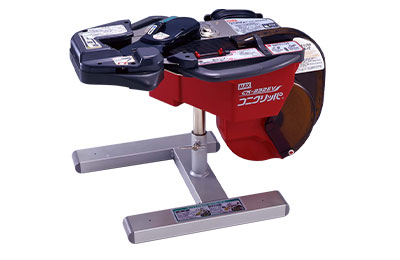
"CONI-CLIPPER" a bag closing machine for vegetables and fruits is released
2000
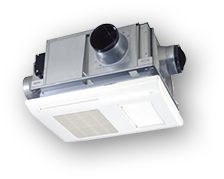
The Concrete Tool Business and the Housing Environment Business were newly added to MAX's lines of business. Also, MAX has been working on developing battery operated tools, which are highly anticipated by our customers.
- 2000
- Issued 2,000 yen bill
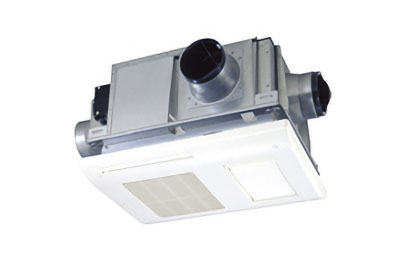
Acquired 2 companies of SHINWA HI-TEC group, which makes heater-ventilator-dryers for bathrooms, and entered into the housing environmental equipment business.
- 2002
- FIFA World Cup in Japan and Korea
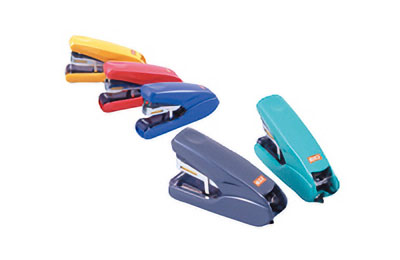
"HD-10DFL" staplers to commemorate the 50th anniversary is released
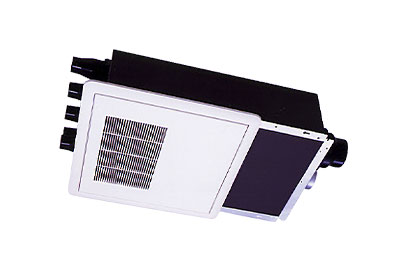
"ES-8200" Total heat exchange type ventilation systems
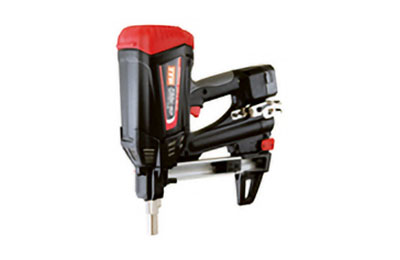
Japan's first "gas nailer" is released
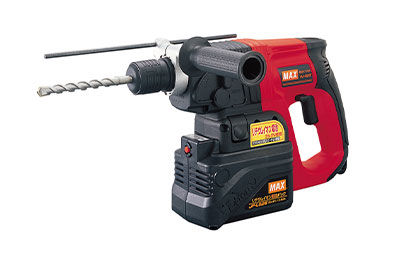
"Hammer drills" concrete tools for professionals is released
- 2005
- Expo 2005, Aichi, Japan
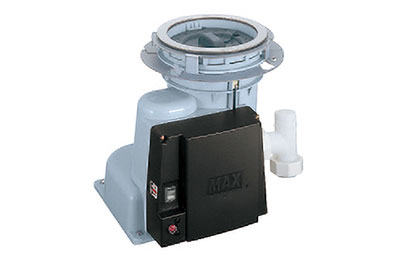
"Disposer systems" for housing is released
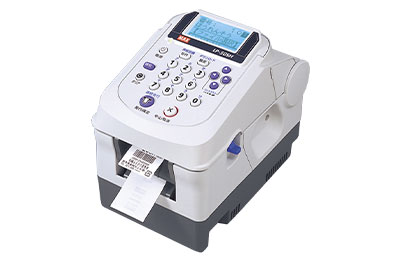
"Thermal label printer" for food labelling is released
- 2008
- Lehman shock
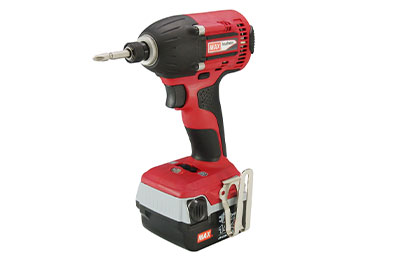
"Impact driver" a rechargeable brushless equipped with a Li-ion battery is released
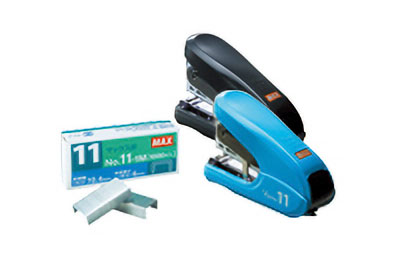
"Vaimo 11 series" a new generation of stapler that can staple 2 to 40 paper sheets with less effort by using staples, creating to a new standard is released
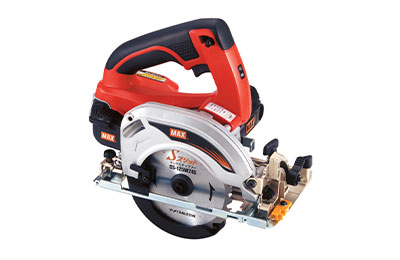
"Rechargeable Circular Saw"14.4V rechargeable tool series is released
2010
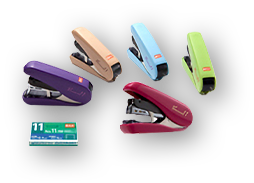
MAX has further evolved staplers by focusing on "binding".We have developed PAPYLER, a paper staple stapler, for workplaces where metal staples cannot be used.
- 2010
- The planetary probe Hayabusa returns to Earth.
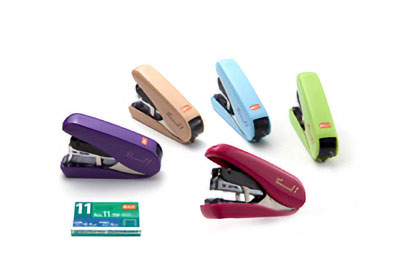
"Vaimo11style" focusing on style and color is released
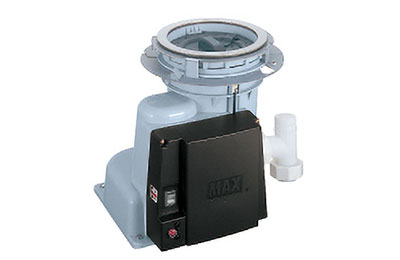
"Disposer systems for detached houses" is released
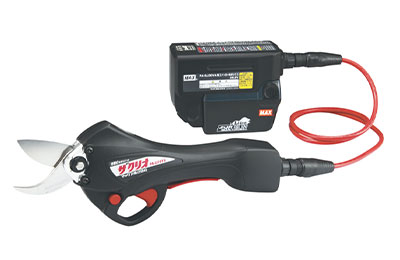
"ZAKURIO" rechargeable pruning scissors is released
- 2011
- Great East Japan Earthquake
- 2012
- Tokyo Sky Tree opened
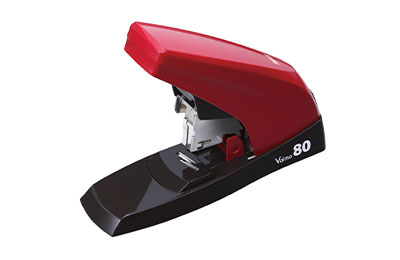
"Vaimo80" the smallest and lightest desktop stapler in its class, capable of stapling from 2 to 80 documents with a single type of staple is released
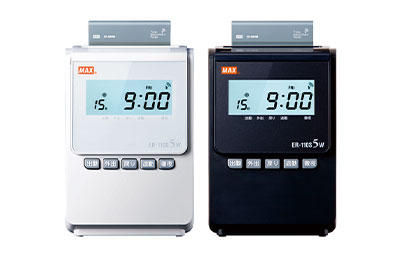
Time recorders "ER-110S5W" and "ER-80S2W" with a new removable radio-controlled clock "T.A.P." as standard equipment is released.
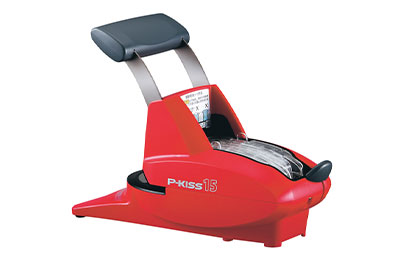
"PAPYLER" a stapler using paper-made staples is released

"TWINTIER" a concrete reinforcing bar tying machine is released
Staplers are commonplace nowadays, but in fact they have undergone many improvements based on customer voice. Here we introduce the history of staplers, along with the background to their development.
1940

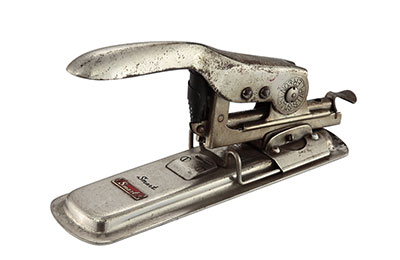
Our "Yamako Smart" appeared on the scene soon after the war, when staplers were still a rarity. Until then, documents were typically bound by drilling holes through the sheets of paper and tied with a string. The stapler is commonplace today, but in those days it was a truly revolutionary product.
In fact,WeI heard that the stapler was also called the "Three Sacred Treasures" of the stationery world.
1950
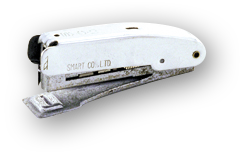
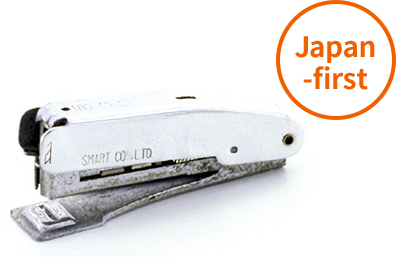
The "Yamako Smart" was groundbreaking for its time, but it was also quite large and expensive. For this reason, it was widely adopted for shared use in the workplace.
Thus, Max began developing a more compact stapler, with the idea of enabling everyone to have their own stapler. This was how Japan's first handy stapler, the "SYC-10," was born. At just ¥200, less than half the price of the Yamako Smart, staplers became more and more widely used, transitioning from an office product to a personal tool.

After the company changed its name to MAX, the "SYC-10" was rebranded as the "MAX-10." As staplers became increasingly popular, "MAX" became synonymous with "stapler." When they wanted to buy a stapler at a stationery store, many people simply asked for a "MAX."
Eventually, in 1967, after continuous improvements, our staplers and staples were certified under Japan's system of industrial standards, JIS.
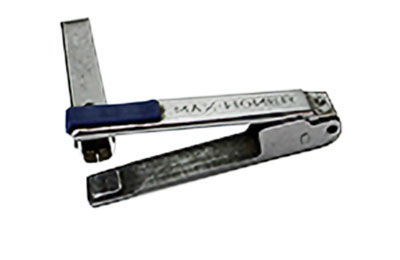
A stapler that can be used horizontally as well as vertically for saddle stitching.
Staplers are often used as stationery, and they are also used in many other ways around us.
A variety of staplers have been developed based on customer feedback. The shapes have been improved to be easier to use depending on the purpose.
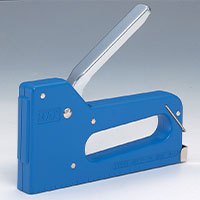
A stapler that can be driven into wood, useful for various tools such as attaching posters and cloth to chairs. It is used in place of small nails.
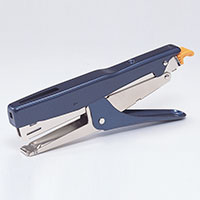
The stapler can be used at dry cleaners to fasten tags on laundry, or to bind paper bags and plastic bags. Easy-to-grip pliers type stapler.
- *The photos in this column are from a current sale.
1960
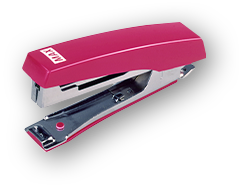
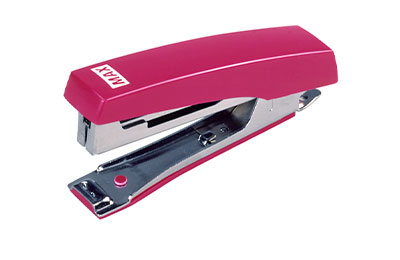
The HD-10D was praised for its design focusing on operability and durability. It later became a popular standard product.
1970
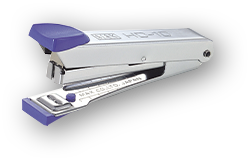
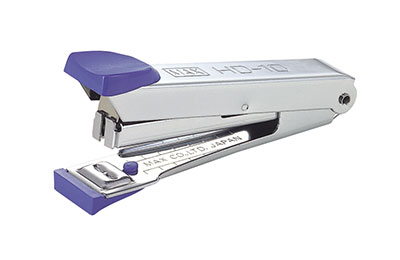
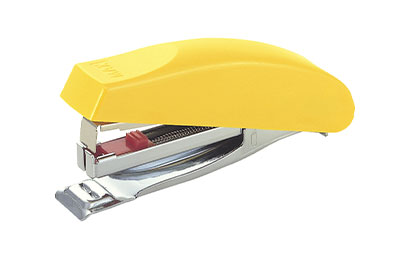
Although MAX made many innovations to staplers over the years, it went back to basics, to focus on "binding." We felt that stapling paper pages together should be much easier.
After much trial and error, in 1979 we developed a "light effort" mechanism that applied the physics of levers to reduce the force needed to operate the stapler. It was now possible to use a stapler using half the force previously required, so even young children could use a stapler effectively.
1980
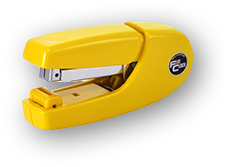
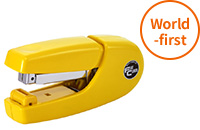
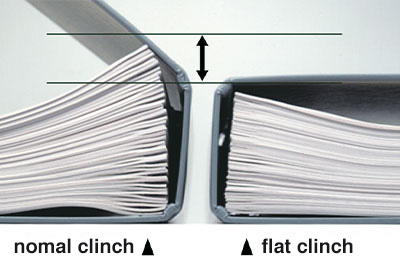
It simply means that the legs of the staples are bent flat against the bottom of the stapled sheets.
MAX developed this world-first technology based on some feedback from a user who reported flattening staples with a hammer to reduce the bulkiness of stacked documents. Flattening the legs of the staples helped to slim down the piles of papers and save substantial storage space.
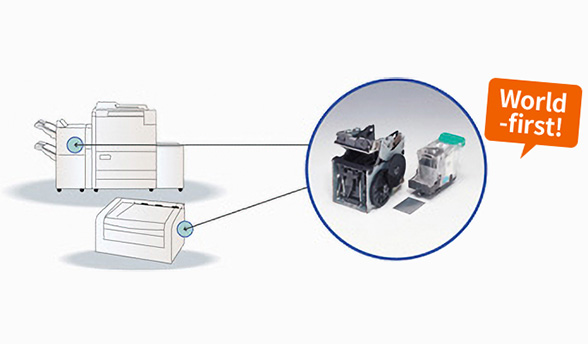
Stapling is one of the functions of printing and copying. This function has become common knowledge for business people, but it is also a technology developed by Max for the first time in the world.
The "Auto Stapler" was designed for people who often create large volumes of documents, and is supplied to many MFP manufacturers on an OEM basis.
1990
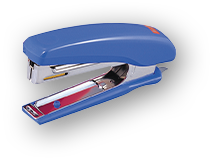
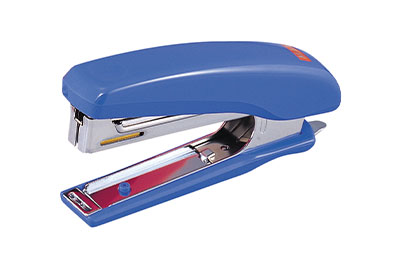
The "HD-10D," which was introduced in 1968, enjoys a total redesign, including a one-touch function that makes loading staples very easy.
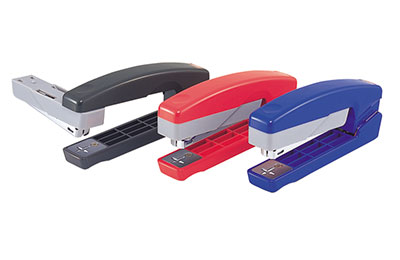
"Hotchkuru" stapler can be used not only as a standard stapler but also as a saddle stapler. It was developed in response to customers' requests to make small booklets. It can also be used for paper crafts and paper box stapling, making it a very popular stapler.
There are still some unusual staplers today, such as the "Hotchkuru," which can bind horizontally and vertically, but there were many unique staplers in those days. Here we will introduce some of them.
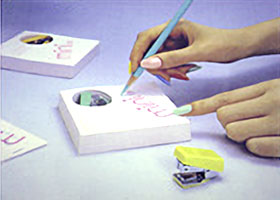
Ultra-mini size of 26mm (length), 35mm (width), and 17mm (depth).
It is a compact yet powerful stapler that can use size 10 staples and can also be used for tacking. Available in five lovely pastel colors, it was a very popular product, especially among young women.
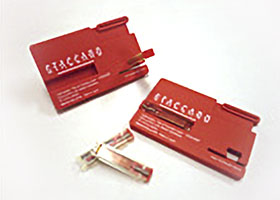
This unique stapler was released during the heyday of credit cards, telephone cards, and other cards.
It was thin and light, only 6mm thick, so you could gently pull it out of your breast pocket and be the talk of the town!
Card-type punches were also sold at the same time.
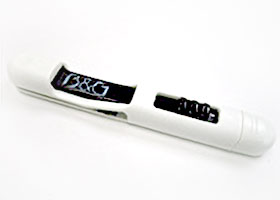
A bar-type stapler whose tip opens and closes by sliding the button in the center of the main body. It comes in two colors, white and black. B&G" stands for "Boys & Girls," and "L&G" (Ladies & Gentlemen) was also released as a sister product.
- *Not available now.
2000
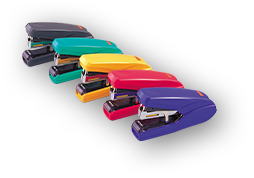

Equipped with "light effort" and "flat clinch" mechanisms, this No. 10 stapler was capable of stapling together up to 26 sheets of paper. It was developed and sold as a commemorative model to mark the 50th anniversary of the launch of MAX's first ever handy stapler.
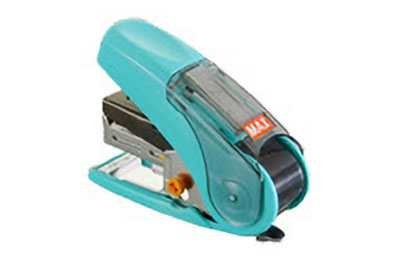
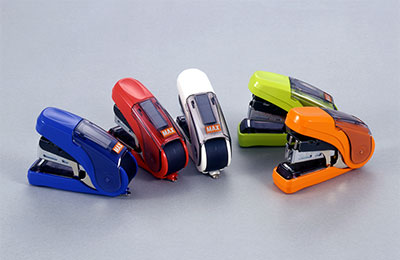
These staplers, originally targeted to women and elderly users at the time, were developed with an emphasis on enabling easy, reliable stapling with one hand. "SAKURI" series was highly rated because it required 50% less force to operate and for its ability to store 100 spare extra staples. "SAKURI Flat" a model in the series equipped with a flat clinch mechanism, won a "Stationery of the Year" prize at the International Stationery & Office Products Fair (ISOT2007).
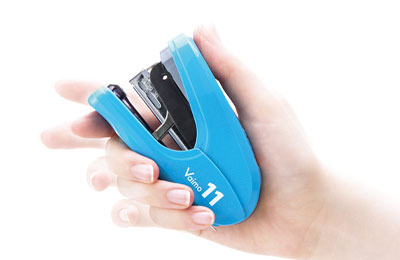
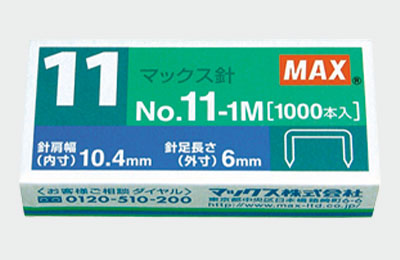
Our marketing manager at the time was riding the bullet train on a business trip. She observed a woman dressed in a suit breathing heavily as she used a desktop stapler to prepare a number of documents. After hearing the opinions of actual desktop stapler users, MAX set out to develop a compact stapler capable of matching a desktop stapler. Thus, with " the development of a new "No. 11" staple specification, along with a "light effort" mechanism, the new "Vaimo11 FLAT" was born. It was capable of stapling together 2 to 40 sheets of paper.
2010
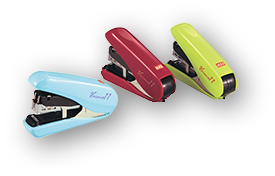
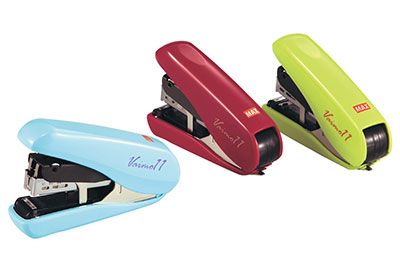
"Vaimo11" was launched in 2008, and while its functions were highly satisfactory, some women with small hands said that they wished the body could be smaller.To address this issue, we designed the "Vaimo 11 STYLE" with a slimmer body and a more rounded design that fits women's hands more comfortably, while maintaining the high functionality of the Vaimo. Female employees took the lead in deciding on colors, and narrowed down the choices from among many samples. The result is a design with women in mind.
In Japan, the mainstream stapler is a nipping and tucking type, but in fact, the usage and name of stapler varies from country to country.
Here, we will use the stapler sold by MAX as an example.
In Southeast Asia, the handy type stapler is the most common type, just like in Japan. Incidentally, in Thailand, staplers are called "MAX."
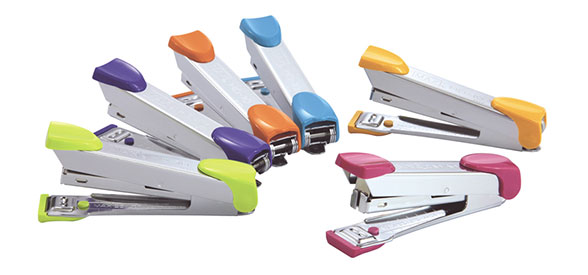
In the U.S., many people use a "desktop" type stapler, which is slightly larger and sturdier than its Japanese counterpart. In English, it is called a "stapler."
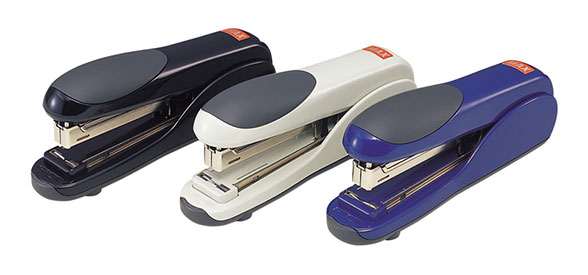
In Europe, the pliers type stapler is used, which is held like pliers. The Italian word for this type is "cucitrici."
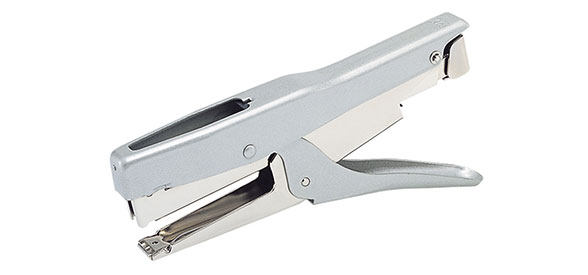
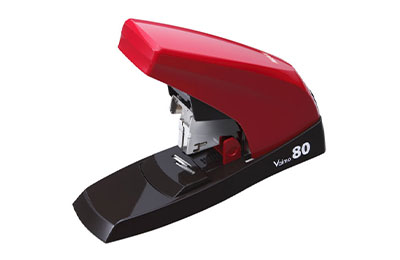
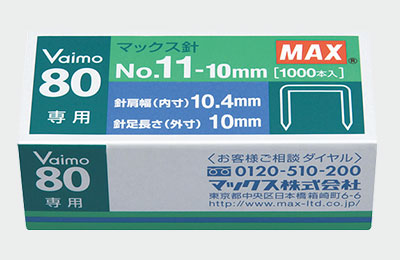
Until this time, desktop staplers were typically shared between multiple people, but with various innovative features, such as compact size, light weight, and improved binding, the "Vaimo80" broke new ground in ease of use. Featuring advanced technology such as a mechanism to deliver maximum lever motion and strength for stapling, as well as a new staple design specification. The Vaimo could bind from 2- to 80-sheets of paper documents with a third of the effort previously needed to operate a stapler.
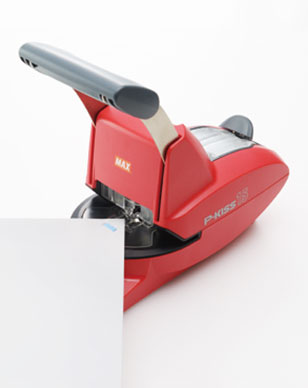
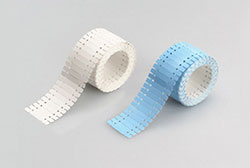
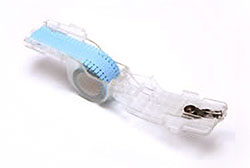
The stapler is an indispensable stationery item in every home and office, but there is one office that actually needs to refrain from using staples.
This is a food company.
Starting in the 1990s, the use of metal staples in the food industry was gradually phased out for safety reasons, and later banned entirely to prevent contamination.
This inspired MAX to think about stapling paper with paper. After seven years of development, MAX released this product. Since the staples are made of paper, there is no need to separate paper and metal when disposing of office documents. With the paper staple staplers allowing restapling without any noticeable trace of the previous binding, we look forward to developing more paper staple stapler products in the future.
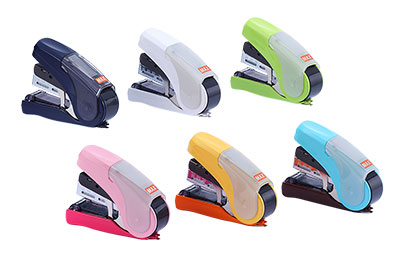
The compact stapler "SAKURIFLAT," which staples flat with light force, has a lovely two-tone design inspired by sweets, and achieves a maximum stitching capacity of 28 sheets.
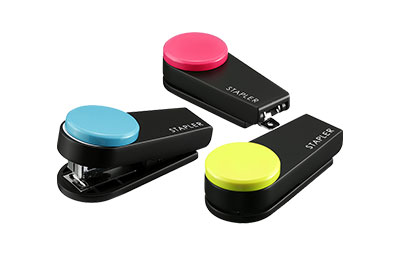
The compact design allows you to carry it in a pen case or pouch. The design of the round button is inspired by the color palettes used by professional make-up artists. Even though it is small, it expresses the trustworthy image of a professional tool and the joy of beautiful colors.The product won the Good Design Award in 2016 and the Excellence Award in the Design Category of ISOT2016 (International Stationery & Paper Products Exhibition).
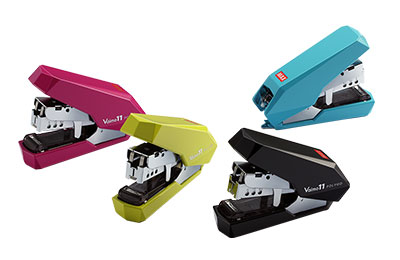
While maintaining the performance of the previous "Vaimo 11," the new "Vaimo 11" is small enough to fit in a small hand.
The new "Vaimo 11" features a polyhedron design, which is a departure from the rounded design of many previous models. Each edge is cut in the image of a diamond, expressing stylishness and a sense of luxury. The vivid colors are sure to look good at the office! Recommended for those who are particular about not only functionality but also design.
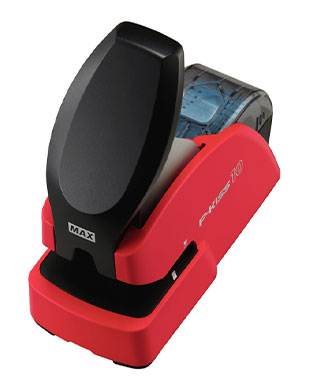
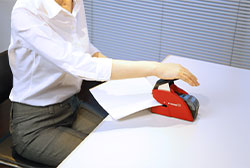
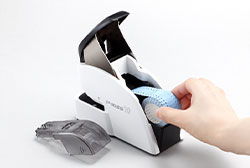
The design of the "P-KISS15," released in 2013, has been completely revised to achieve a size that can be placed on a personal desk. The number of sheets that can be bound is from 2 to 10, which is frequently used. Although it is a paper needle, it has received high praise for its "firm binding" and "re-fastening" features. In addition to food companies, this product is now being used in schools and government offices because it does not require separate disposal, and in kindergartens and nursery schools because there is less risk of injury.
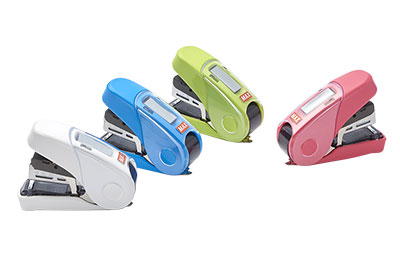
It can bind up to 32 sheets with a No. 10 needle, and pursues a clean binding shape and greater ease of use.
This is the third model in the popular Sakuri series with its compact size and light weight. It is becoming a standard stapler following the familiar HD-10D.
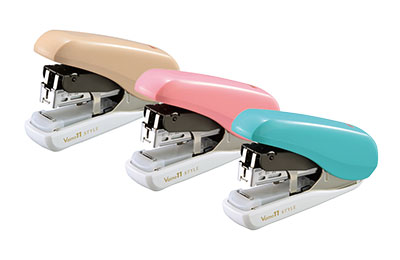
The Vaimo11 STYLE is the slimmest stapler in the Vaimo11 series.
The slim body is easy for women and people with small hands to grip, and the two-tone color scheme of fresh beige, pink, blue and white will brighten up your desk.
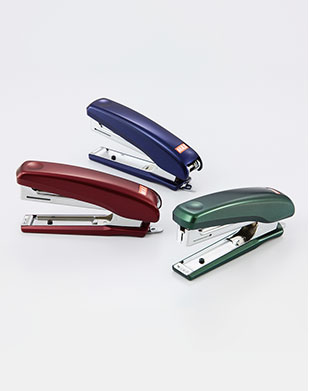
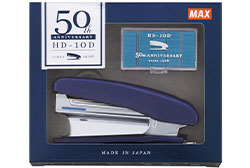
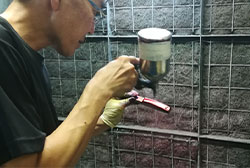
The first model of the HD-10D was released in 1968 with emphasis on operability and durability, and the second model was released in 1991 with a one-touch open function for easy staple loading and a curved design that fits comfortably in the hand. Since the stapler has been used as a standard stapler, we sold a limited number of models to commemorate its 50th anniversary.
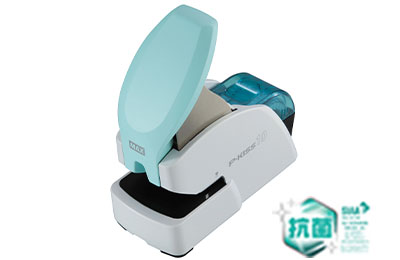
This is an antibacterial model of the "Papyler" series of paper staple staplers, featuring special staples for paper materials.
A plastic material with antibacterial properties is used for the handle, body cover, and staple cover, to ensure safety even after frequent contact with various human hands. This is the only MAX stapler certified to carry the SIAA mark.
To celebrate the 11th anniversary of the Vaimo11 series, we collaborated with BOX&NEEDLE, a long-established paper container manufacturer in Kyoto. By binding the richly textured washi paper for the paste-up box with "Vaimo11," you can create your own storage box for staples and other items. The Vaimo11 series will continue to be one of MAX's mainstay products, and we will continue to develop a variety of products.
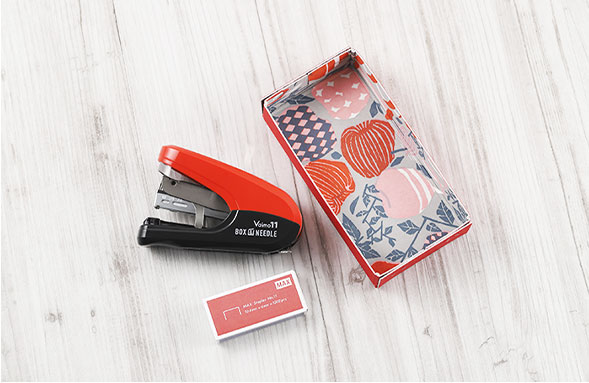
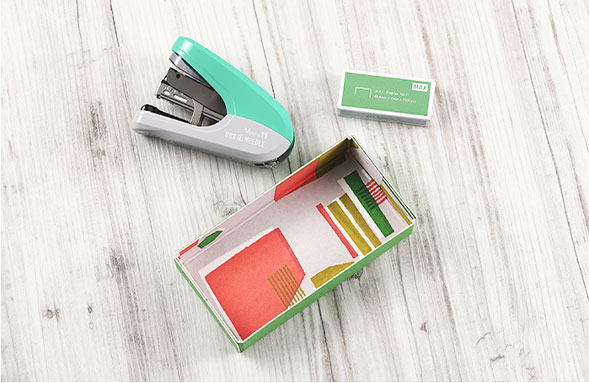
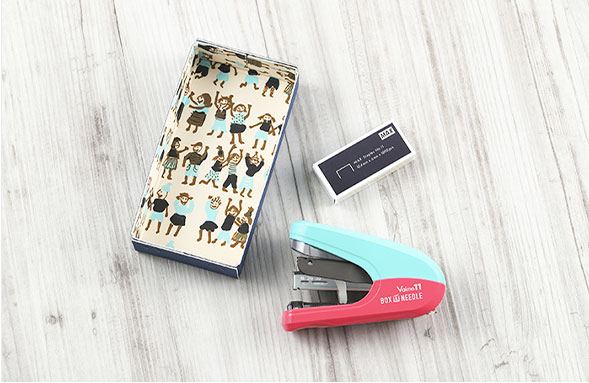
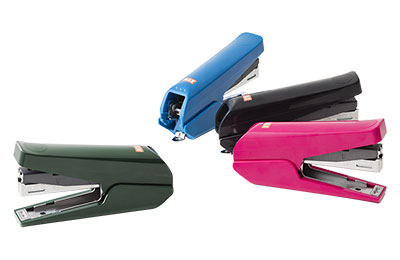
The "variable double-force" mechanism is a technology that varies the lever ratio to enable the "light effort" mechanism to function with pinpoint precision after the staple starts to penetrate the paper.
This design enables light effort with minimal stapler height. The stapler is also equipped with a long magazine holding 150 staples, capable of binding to a depth of 53 mm.
Selected as one of the "Good Design Best 100" in 2019 by the Good Design Award for its outstanding design and functionality in Japan.
More and more users are choosing stationery not only for its function but also for its design. In response to this trend, we have released a stapler with an animal-designed silicon cover in the hope that users will enjoy owning a stapler as well. The stapler is not only cute to look at but also soft and silky to the touch.
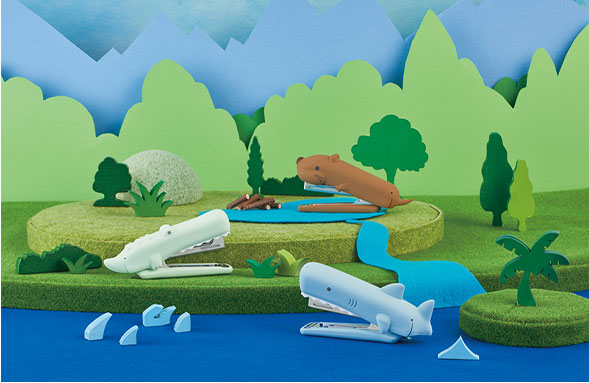
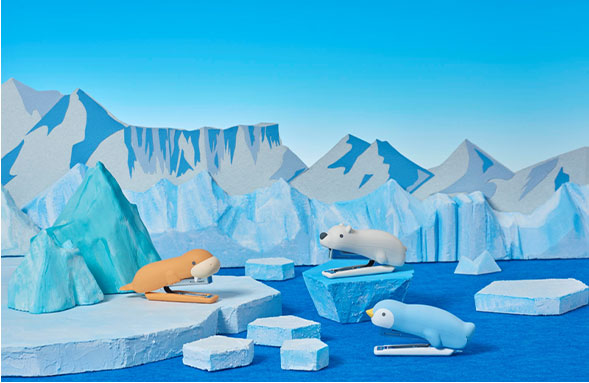
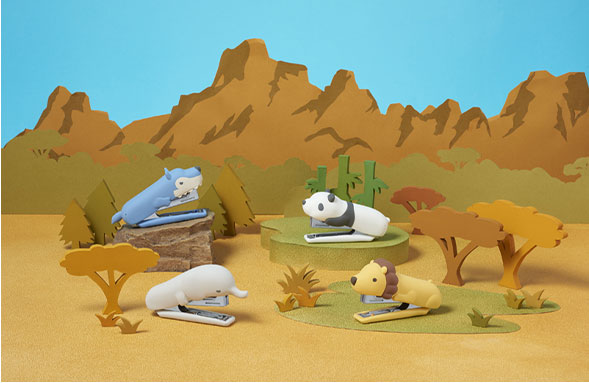
MAX will continue to create products based on customer feedback.
The next product to be commercialized may be the stapler that solves your problems!
Nailers are now an indispensable part of construction sites. In fact, did you know that nailers were not originally developed for use in construction?
We will introduce the history of building and construction tools and the history of construction sites, which have evolved based on "customer voices.
1950
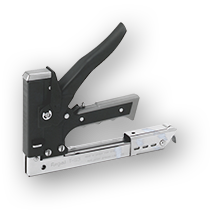
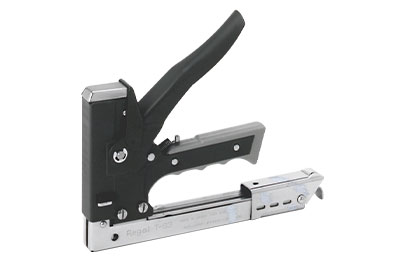
After MAX began producing office staplers immediately after the war, the company grew steadily as a maker of stationery and office equipment.
With the aim of expanding its range of stationery and office products further, MAX released a staple gun that used staples instead of thumbtacks to put up posters and other items.
Although the product failed to become popular as an office tool, it became an essential item for plasterers, for fixing laths.
1960
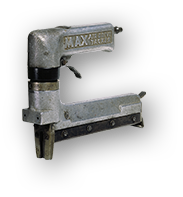
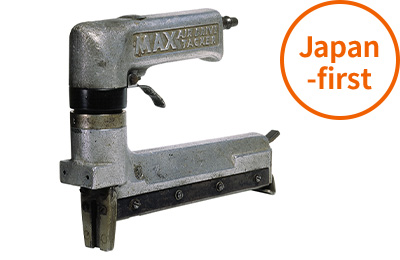
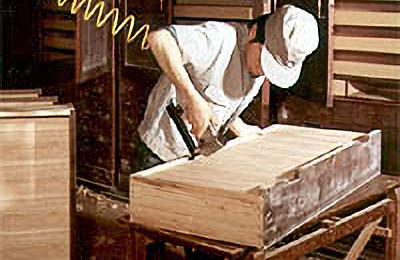
At this time, most of the work done by furniture makers such as "flush coring" (joining the wood core material inside furniture doors) and chair upholstery was done by trained craftsmen who would hold nails one by one in their mouths before hammering them in.
This was a time of economic boom when the Japanese government was planning to double their per capita income. With an expanding housing market and increasing numbers of marriages, the furniture industry was growing fast, so there was a surging demand for nailers.
- *1Staples, used in industrial tools such as nailers, are inserted in the same shape as a staple to join parts.
- *2The name "air tacker" has now been unified to "air nailer.
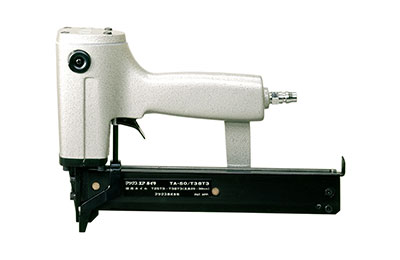
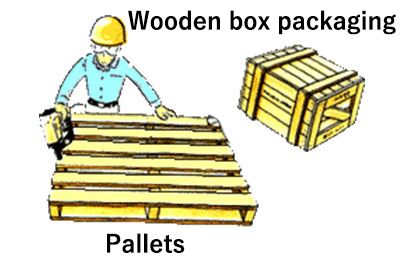
In the late 1965s, the export industry was in the spotlight. Export goods required large wooden boxes for packing. This is what is known as heavy duty packaging for export. A nailer was essential for its production, and at that time, nailers made overseas were used.
Max developed the TA-50, a large nailer that uses T-nails, and entered the packaging market as well.
1970
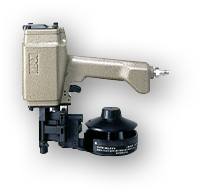
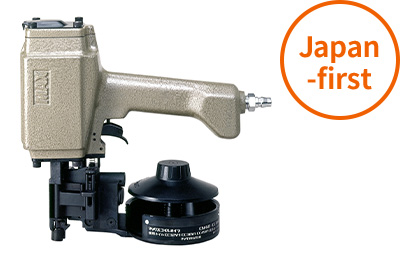
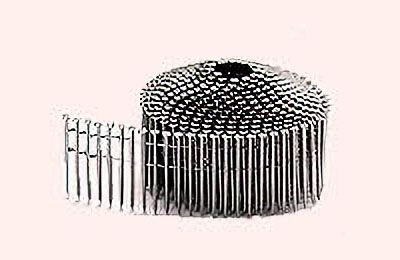
"Coil nails" are round nails welded together with wire to form a collated coil of nails.
At this time, nail guns used in the packing industry was typically using T-nails. Since the round headed nails used in manual nailing work were stronger than T-nails, there was a strong market demand for a nail gun capable of handling round head nails.
The CN-60 was the first nail gun that could drive in round nails to a depth of 45 mm. Its performance was so outstanding that the whole packing market moved rapidly to the use of round nails.
The nailer's ability to drive round nails made it popular in the packaging market, and the next target was the housing construction market. However, here we hit a thick wall. The traditional Japanese housing construction method prided itself on not using nails to join pillars at the joints. Therefore, at that time, we could hardly get carpenters and hardware dealers to pay attention to us.
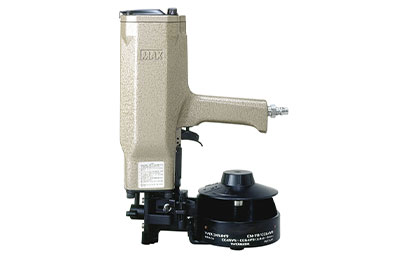
In 1973, there was an unprecedented building boom. Carpenters were so busy that they finally started using nailers.
In 1974, in the midst of the oil crisis, the North American 2×4 construction method was approved by the Ministry of Construction, and the 2×4 construction method, also known as the "nailing method," was able to greatly appeal to the public as a powerful tool for construction sites.
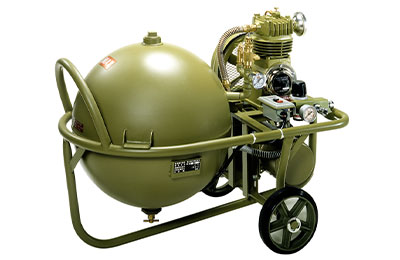
1980
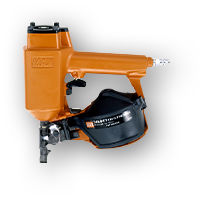
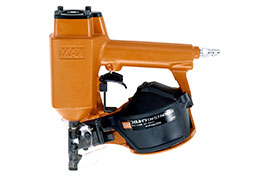
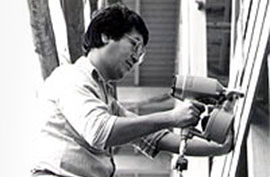
The popularity of air nailers has exceeded 10%, making them a necessity for carpenters.
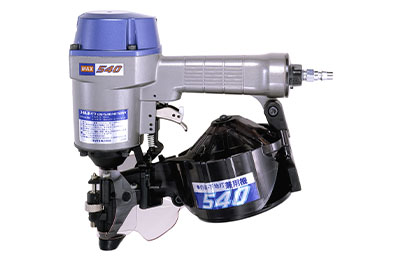
Hit products that have established their current status.
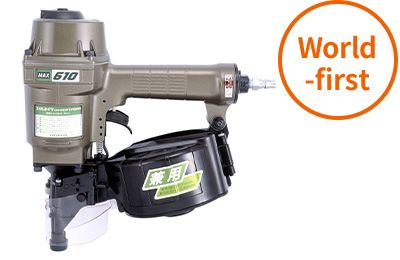
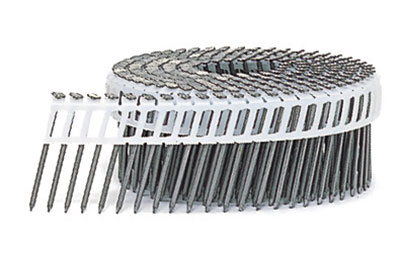
At this time, sheet metal workers in the construction industry were complaining that wire collation were dangerous. Due to the risk of wire injury and because fragments of the wire would sometimes protrude beside the nails driven into the work surface, MAX solved these problems by developing plastic connection sheets.
These sheets prevented wire injuries and offered an attractive finish, to the point that plastic sheet connections are now the standard throughout the industry.
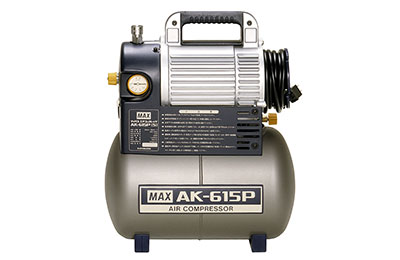
At that time, the mainstream compressors for construction were large ones that could be lifted with both hands. The AK-615P, however, could be lifted with one hand. It exploded onto the market.
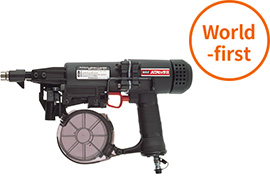
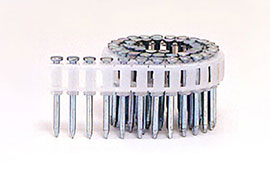
1990
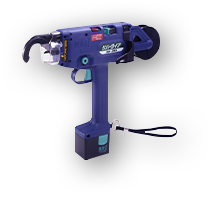
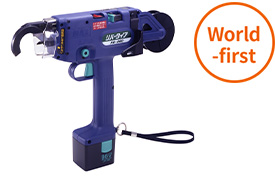
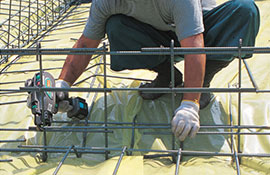
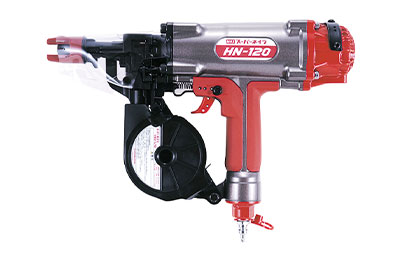
Today called the "High Pressure System", using three times the air pressure of previous nailers, the MAX "Super Nailer" was designed to deliver a powerful driving force, in a compact, lightweight matter.
Around 1.4 to 1.5 million homes a year were being constructed in this period. The number of active building carpenters in Japan was estimated to be 450,000 at the time. *From 1991 business statisics
Products like the Super Nailer were marketed with a long-term view, in the sense that they could help meet the demand for efficient construction work despite the expected decline in population and in active building workers.
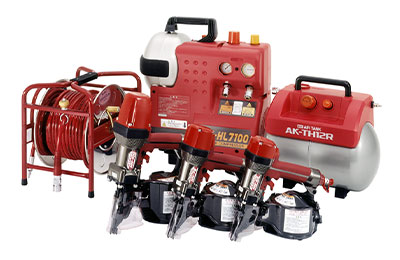
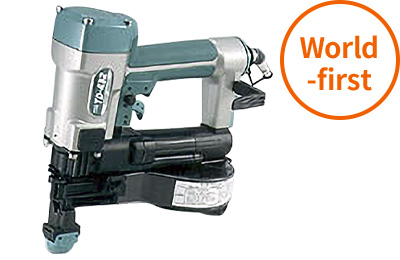
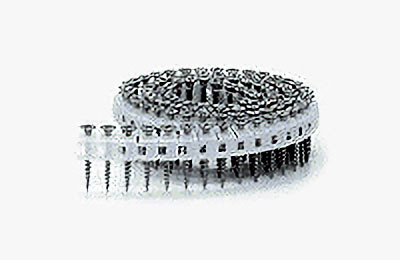
As homes were becoming more luxurious and sophisticated, the lessons of the Great Hanshin Earthquake prompted demands for improvements in seismic performance.
This became the background in why there was an urgent push to start using more screws for joining plasterboard in building interiors.
MAX addressed this change promptly, by developing the world's first air-driven "Turbo Screwdriver" to drive in and tighten screws pneumatically.
Compared to conventional electric screwdrivers, the Turbo Screwdriver made the work of tightening screws amazingly light and speedy.
2000
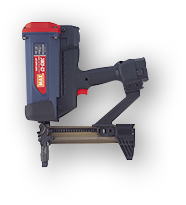
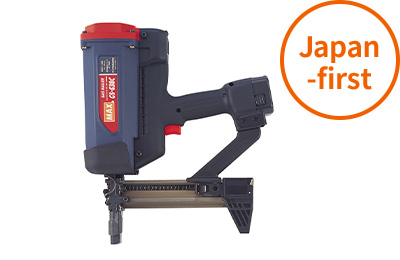
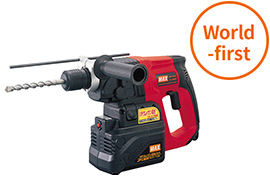
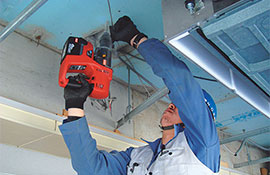
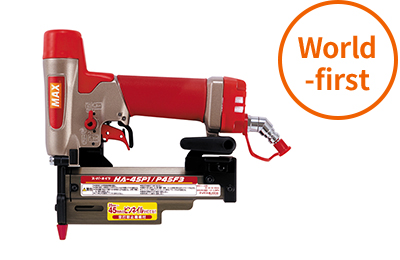
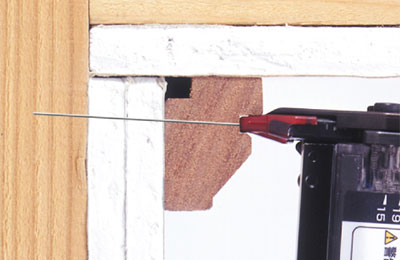
A pin nail is a nail as thin as a Western-style sewing needle. Imagine this. A 4.5 cm long needle is driven straight into a tree. It's too thin, too long... like it would bend in the middle of hammering...That's what we've done with the HA-45P1! Pinnails are small nails with nail heads that are used for flooring around edges and baseboards. However, in fact, 92% of the pinnails used in the market are 35mm or less in length, and only 8% are 45mm or longer. *Calculatid from our shipment results in 2011.
But! In 2006, MAX responded to the voices of customers who were having trouble with even a small amount of pinnails, and also reacted sensitively to changing construction methods, and launched the HA-50P1, which can drive nails up to 50mm.
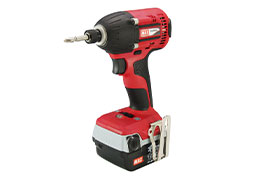
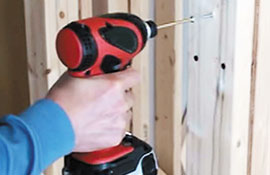

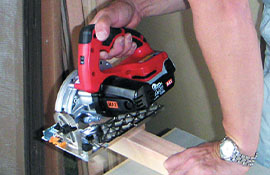
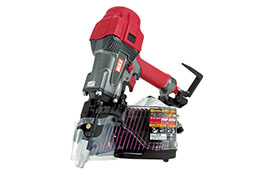
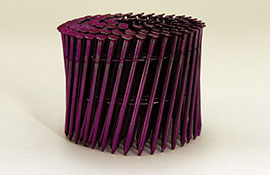
Since the invention of the "Super Nailer", the world-first high-pressure nail gun developed by MAX in 1994, these nail guns have been enjoyed and supported by customers. We will continue to develop and offer products to meet the demands of increasingly diverse construction methods and materials.
2010
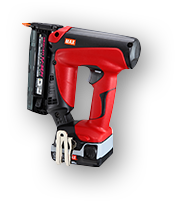
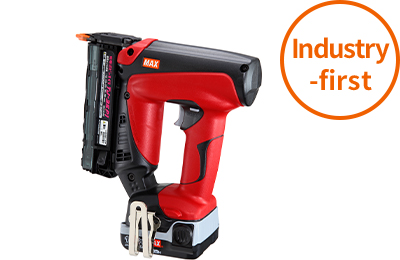
The industry's first "recoil-absorbing mechanism" suppresses recoil during hammering, reducing the loss of force and achieving a beautiful finish without nail lifting even with light pressing.
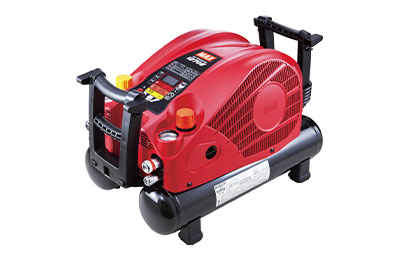
With an "AI mode" that reduces the noise generated during air compression without reducing the discharge flow rate, which is directly linked to nailing efficiency, MAX was able to develop a very quiet compressor. Thanks to comprehensive motor improvements that also enables optimized automatic control by detecting the air use volume in real time, the compressor product had both excellent energy-saving performance and durability.
In 2017, this product evolved into the AK-1270E2 series, equipped with remote operation via smartphone, an industry-first feature.
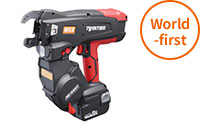
Equipped with the world-first mechanism to ties by feeding two wires simultaneously and twisting them together, achieving a 30% higher tying speed,*1 as well as a "pull back" mechanism that boosts the tying force by 50%*2, and a "wire bending" mechanism that halves the protruding tie height to 12 mm*3, this product increases the efficiency of rebar tying work.
*1-3: Calculated relative to the previous MAX RB-398 model released Oct. 2017.
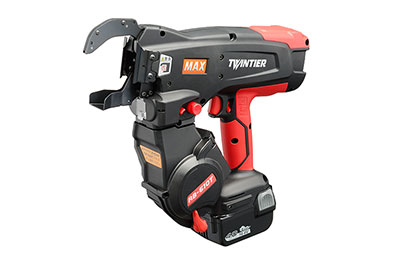
Increasing the target rebar diameter beyond our previous model* makes this tool suitable for use on construction sites that use larger rebar, where manual labor was previously required, e.g., for columns, beams, pressure-resistant slabs, and the substructures of bridge piers.
* MAX RB-519A released in Nov. 2019
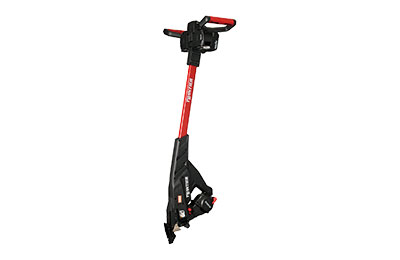
The work of tying rebar for floor surfaces involves extended time in a posture of looking downward and bending at the waist, thus minimizing back pain can be a challenge.
This model, the TWINTIER RB-401T-E, enables the work of tying to be performed in an upright walking position, thereby reducing strain on the back.
Since the tool can be operated with both hands, it also reduces strain in the arms, so handling is ergonomic.
The significant reduction in back strain suffered by workers also helps to improve the workplace environment.
MAX will continue to create products based on customer feedback.
The next product to be commercialized may be the tools that solves your problems!